Pipe thread lathe is also called oil country lathe,thread turning generally refers to the method of machining threads on a workpiece with a forming tool, mainly including turning, milling, tapping, threading grinding, grinding, and whirlwind cutting. When turning, milling and grinding threads, the transmission chain of the machine tool ensures that the turning tool, milling cutter or grinding wheel moves accurately and evenly along the axis of the workpiece by one lead for each revolution of the workpiece. When tapping or threading, the tool (tap or die) rotates relative to the workpiece, and the first formed thread groove guides the tool (or workpiece) to move axially.
And what we are mainly aiming at is thread turning using pipe thread lathes. The thread forming tool or the thread comb tool can be used to turn the thread on the pipe thread lathe. Turning threads with a forming turning tool, hesitant tool structure is simple, it is a common method for small batch production and processing of threaded workpieces. Turning threads with a thread comb tool has high production efficiency, but the tool structure is complex, and it is only suitable for turning fine-tooth short threaded workpieces in medium and large-scale production.
The pitch accuracy of ordinary lathes for turning trapezoidal threads can generally only reach 8-9, but the production efficiency and accuracy of professional CNC pipe threading machine will be significantly improved.
Pipe threading lathe machine is a horizontal lathe specially designed for turning large-diameter pipe fittings. It is characterized by a relatively large through-hole diameter of the spindle (generally above 135mm) and a chuck at the front and rear of the spindle box. , To facilitate the clamping and processing of large-diameter pipes or rods.
Oil country lathe machine generally have a large through-the-hole on the spindle box, and the workpiece is clamped by two chucks at both ends of the spindle to rotate after passing through the through-hole. There are generally two ways to feed the tool: one is the same as the ordinary lathe by the lead screw to drive the slide and the tool holder in the front of the bed; the other is the flat comb on the slide in the center of the bed. The external thread cutting head of the knife (see an automatic opening and closing thread cutting head) cuts into the workpiece and moves forward. Some machine tools for processing long pipes also have workpiece support devices, such as a center frame, a tool rest, and a rear bracket.
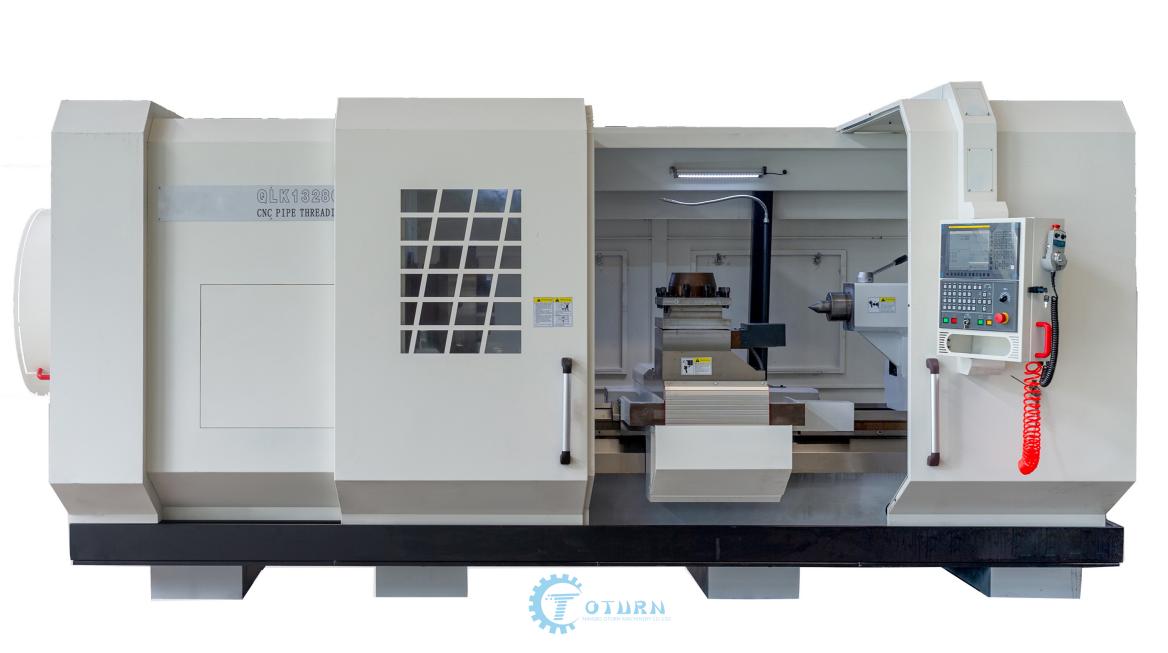
CNC pipe threading lathe recommend
QLK1315 / QLK1320 / QLK1323 / QLK1325 / QLK1328 / QLK1336 / QLK1345 / QKL1353 / QLK1363
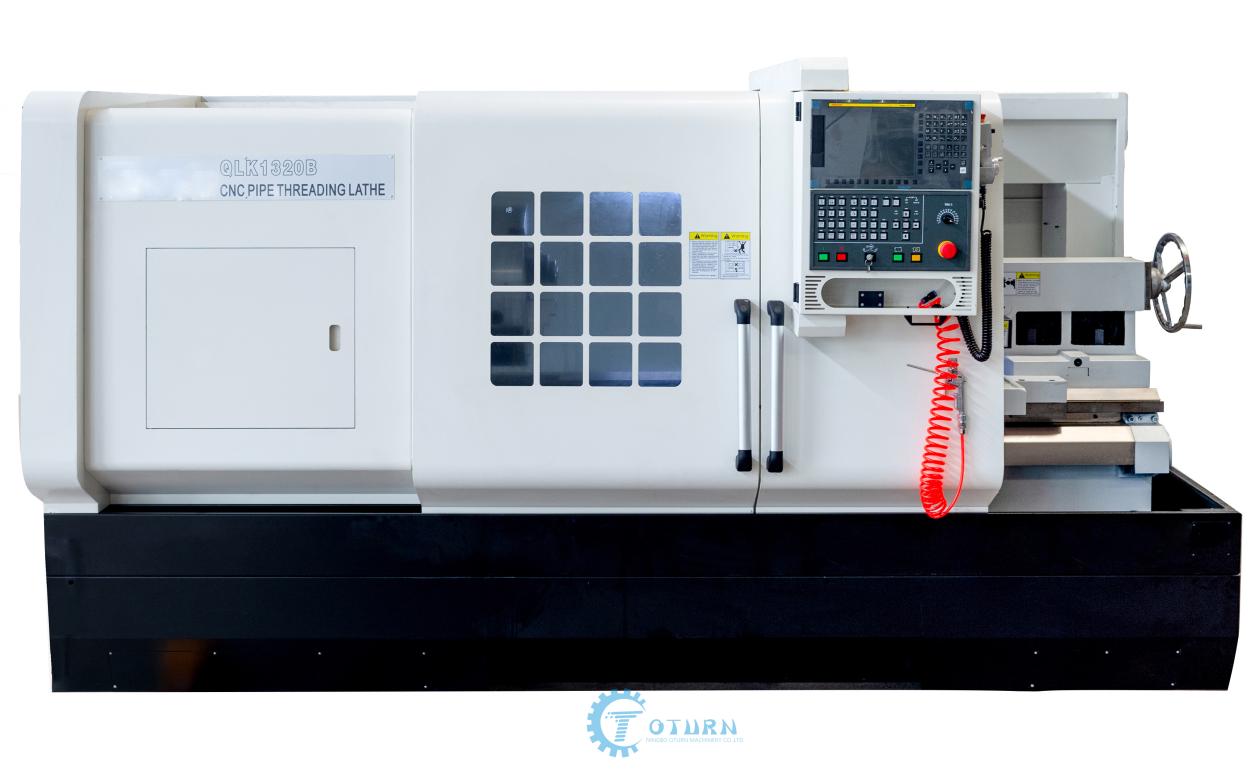
QLK1320
Features of the high quality pipe threading lathe:
1. The bed has an original three-layer wall structure, and the rear wall is arranged with a 12-degree inclined plane, which greatly improves the rigidity of the machine tool.
2. The main transmission chain is graded transmission, which reduces the energy consumption and noise of the machine tool.
3. The use the separate hydraulic boxes, centralized lubrication, and powerful cooling not only reduces the temperature of the spindle but also effectively maintains the cleanliness and lubrication of the spindle box.
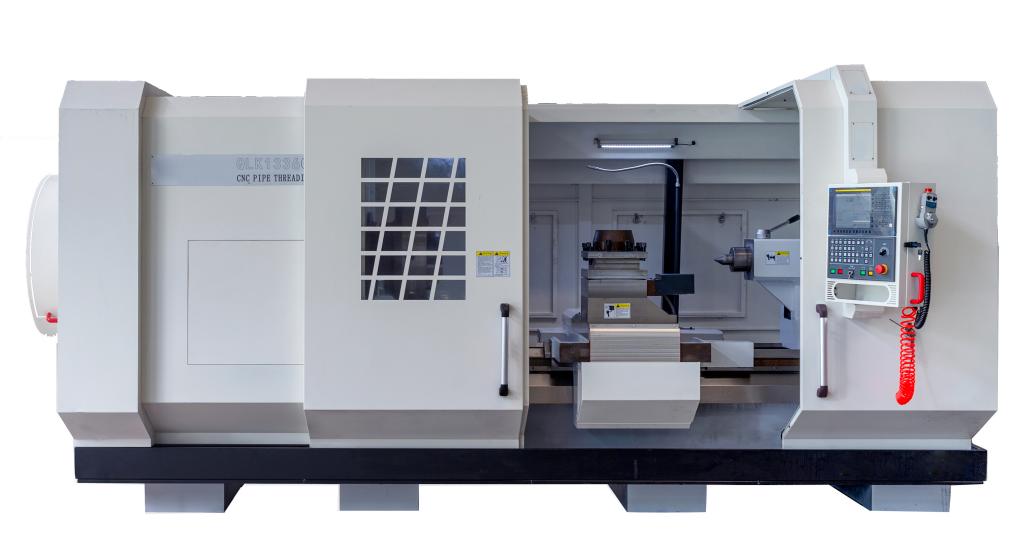
QLK1336
QLK1336 CNC Oil country lathe is a newly designed CNC pipe threading lathe. The main drive is designed to match the rated frequency working range of the selected spindle servo motor. Full stepless speed regulation, wide speed regulation range, which not only meets the requirements of high-speed thread finishing, but also has high cutting efficiency and low noise.
Advantages and benefits of pipe threading lathes
(1)Machine body
The width of body rail is 650mm,material is HT300.Ultrasonic frequency quenching is achieve to HRC52.The roughness is Ra0.63 after grinded by high-precision grinding machine.It has high-precision and abrasion performance. The machine body is an integral structure, which greatly improves the rigidity of machine tool.
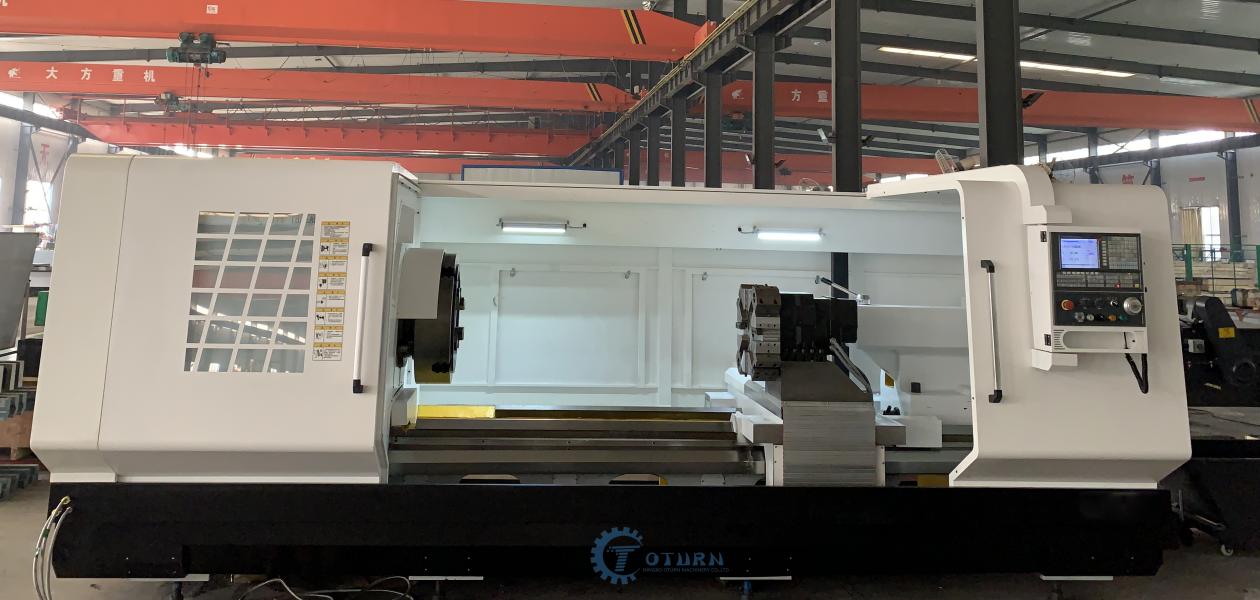
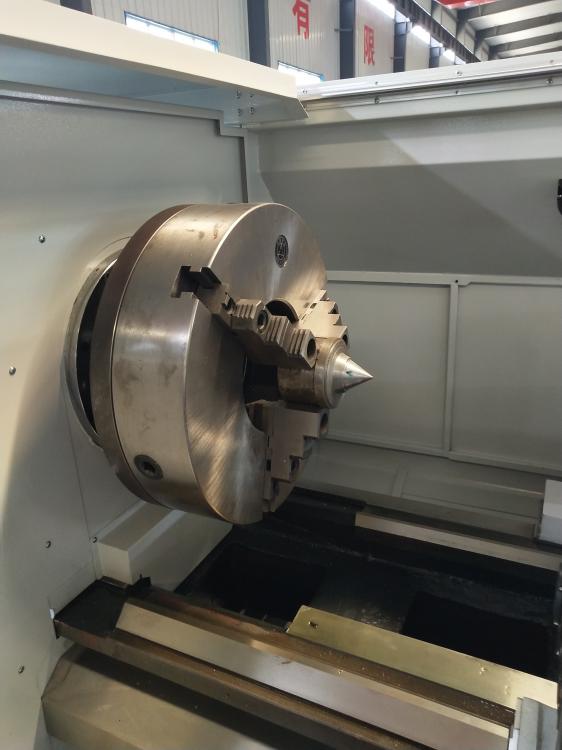
(2) CNC Oil country machines Head Box
Integral gear box type spindle unit, high power spindle servo motor,
Two-speed transmission,stepless speed regulation.
Wide range of speed regulation, not only to meet the requirements of high-speed thread finishing, but also to achieve efficient cutting.Quenched and precision grinding gear, high quality bearings, to ensure the machine low noise, good sound quality.
The spindle box uses the strong external circulation cooling lubrication,
not only reduces the temperature of spindle,but also keeps the cleanness and lubrication of spindle box.
(3)Tailstock
This machine tool is standard withφ120 tailstock spindle. Mohs 6# top.
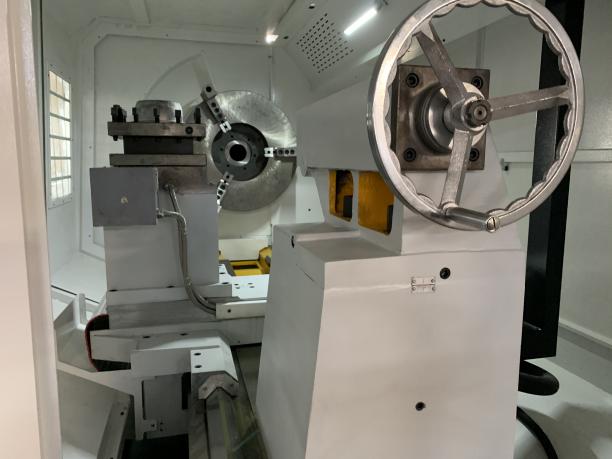
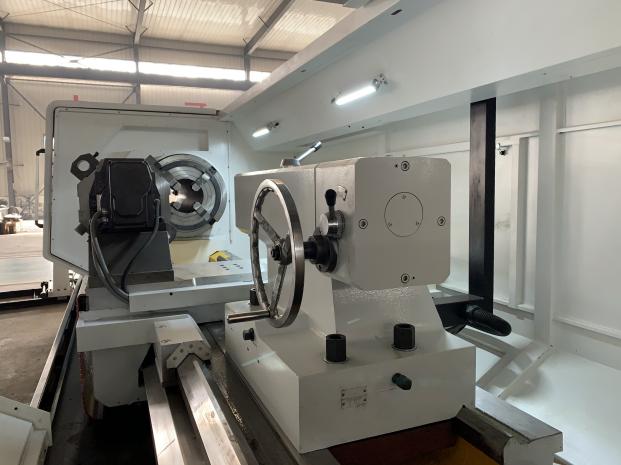
(4)Double-axis feed
Both X axis and Z axis adopt high precision ball screw direct drive and lead screw prestress tension structure. Precision ball screw bearings are used for positioning and supporting; the Z shaft screw nut rack is an integral casting structure.
(5)CNC Turret
Adopts (HAK21280) CNC vertical tool holder . It has the characteristics of high precision, smooth rotation, simple operation and so on.
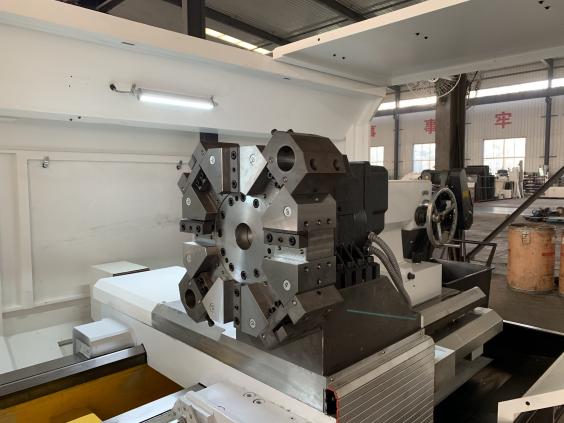
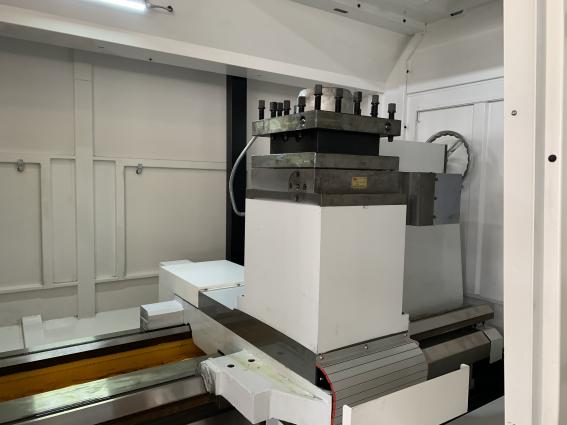
Four reasons to choose CNC pipe threading machine or oil country machining lathe
1.The pipe thread lathe has the characteristics of a high degree of automation, high efficiency and high precision, wide application range, and simple operation.
2.The bedside box is driven by a frequency conversion motor, with a stepless speed change. Spindle bearings from well-known domestic manufacturers, three-jaw chucks from well-known domestic brands.
3.The modular design of the numerical control system is easy to debug and easy to maintain. The x and z axes adopt high-power, servo motors, advanced performance, and strong reliability.
4.It adopts cast bed saddle, slide plate, reasonable internal rib layout, high precision ball screw, high precision, and accurate transmission.
Main Parts Pictures
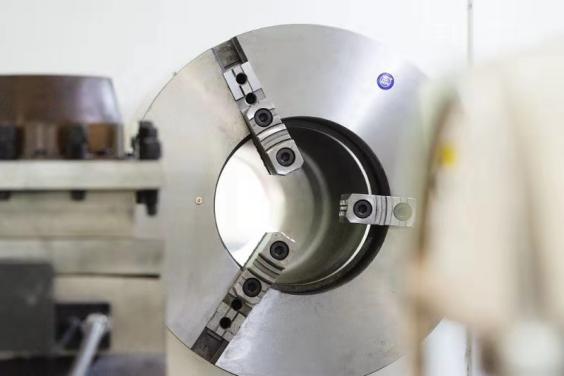
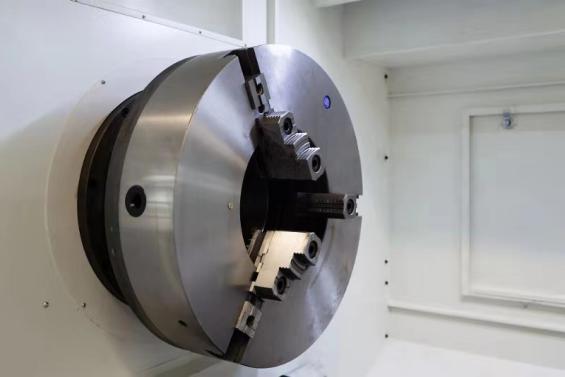
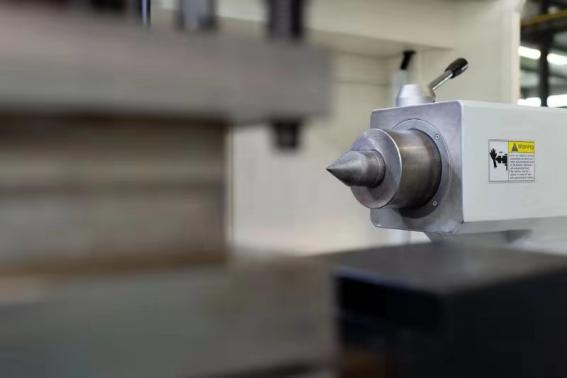
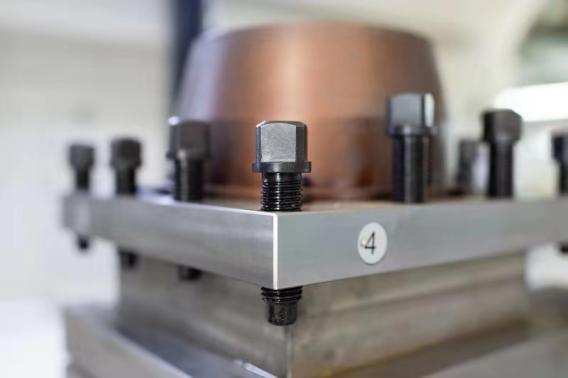
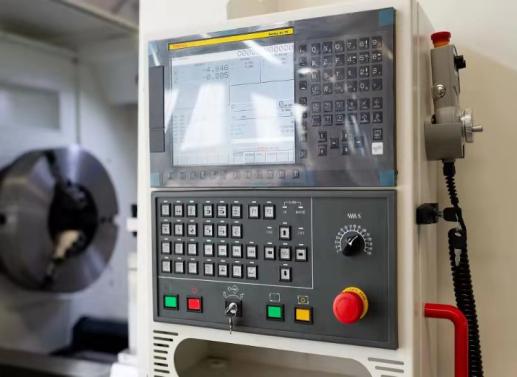
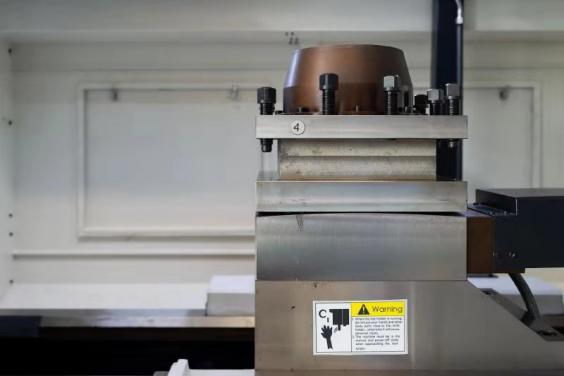
Standard configuration
Four-station electric tool post, automatic centralized lubrication, cooling system, semi-enclosed protective cover.
This product is widely used in mechanical processing operations in machinery manufacturing, petroleum, chemical, coal, geological exploration, urban water supply and drainage, and other industries.
The remaining main parts include drill pipes and couplings.
The petroleum industry is an industrial sector that extracts petroleum (including natural petroleum, oil shale, and natural gas) and refines and processes it. It is composed of oilfield geological exploration, oilfield development and oil exploration, transportation, refining and processing units.
The most commonly used term for tubing in the oil and gas industry is Petroleum Tubing (OCTG). The purpose of petroleum pipes may be different: they may be used to extract or inject gas, oil, water, steam, etc., and can be divided into casings or tubing according to specific applications. Casing is used as a protective layer to help oil wells resist the erosion of internal or external pollutants to maintain durability; tubing is used to inject or extract oil.
Pipe threading machine tools are used to process oil pipes, which are widely used in the petroleum industry. It is a steel pipe used to transport oil and natural gas in oil wells. It is installed in the casing, and oil and gas flow from the oil pipe to the wellhead.
There are two sizes of tubing thread, one is the V-shaped taper pipe thread with dome round bottom with 8 teeth per inch, and the other is the V-shaped taper pipe thread with dome round bottom at 10 teeth per inch.
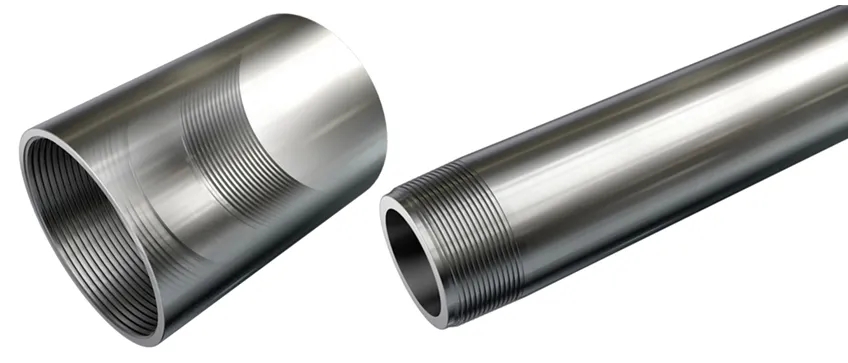
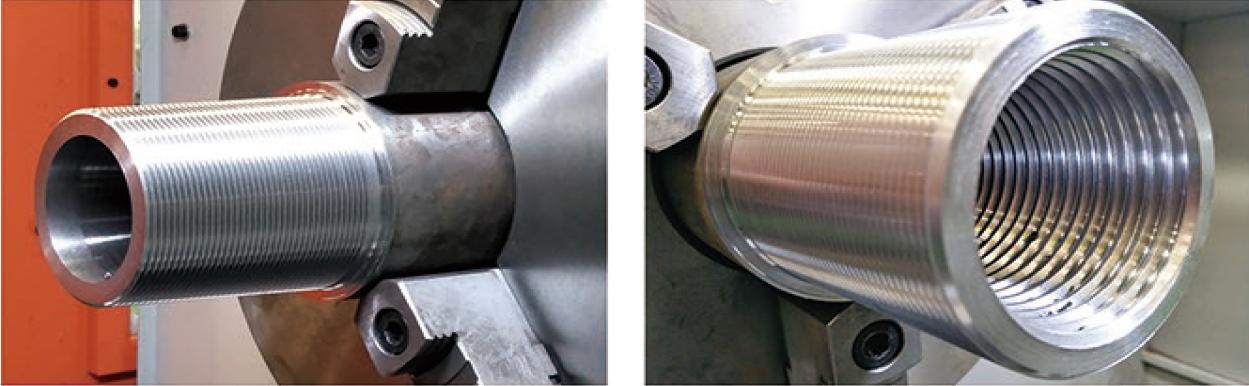

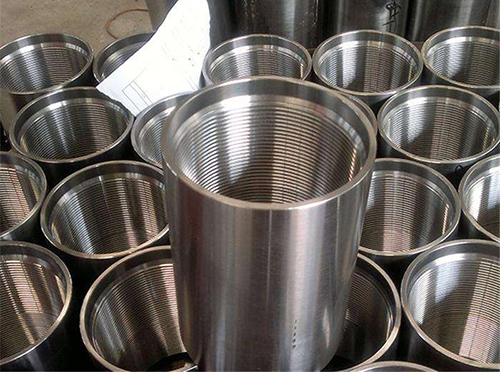
A thread is a continuous protrusion with a prescribed tooth profile formed along a spiral line on the surface of a cylinder or cone. There are many ways to machine threads, and threading is usually used in general machining. When machining threads on a horizontal lathe, the movement relationship between the workpiece and the tool must be ensured. In the actual thread turning, due to various reasons, the movement between the spindle and the tool has problems in a certain link, causing failures during thread turning and affecting normal production. At this time, it should be resolved in time.
How to solve the problem of large roughness, the following are the suggestions of some experienced pipe thread lathe operators:
1. When turning with a high-speed steel turning tool, the turning speed should be reduced and turning oil should be added.
2. Increase the cross-sectional area of the arbor and reduce the extension length (because the arbor is not rigid enough, it is prone to vibration during cutting)
3. Reduce the longitudinal front angle of the turning tool and adjust the clearance of the screw nut of the middle slide plate (the longitudinal front angle of the turning tool is too large, and the clearance of the middle slide screw nut is too large, which will easily cause the tool)
4. When high-speed thread turning, the turning thickness of the last cut is generally greater than 0.1mm, and the chips are discharged perpendicular to the axis direction (when high-speed thread turning, the turning thickness is too small or the chips are discharged in an oblique direction, it is easy to pull the thread flanks).
5. High-end tapping oil or lathe turning oil containing extreme pressure agent should be used to process the thread of the workpiece through the lathe. The use of special metal processing oil can make up for the problem of poor accuracy and low efficiency.
Post time: Sep-21-2021