Conventional lathe machine is a type of traditional lathe machine without control but manual. It has a wide cutting range and can process inner holes, outer circles, end faces, tapered surfaces, chamfering, grooving, threads and various arc surfaces. Conventional lathes are the most widely used type of lathe machines, accounting for about 65% of the total number of lathe machine. They are called horizontal lathes because their spindles are placed horizontally.
Functions:
1. Outer cylinder turning, cone turning, curved surface turning, inner hole turning, end face turning, chamfering and other machining;
2. Metric thread, inch thread, modular thread, pitch thread cutting;
3. Shot and long taper turning;
4. Drilling, boring, jacking and grooving;
5. Left hand turning and right hand turning;
6. Even grinding and milling with grinding and milling attachment.
The main components of conventional machines: bed,headstock,feed box, tool post, carriage, tailstock, and motor.
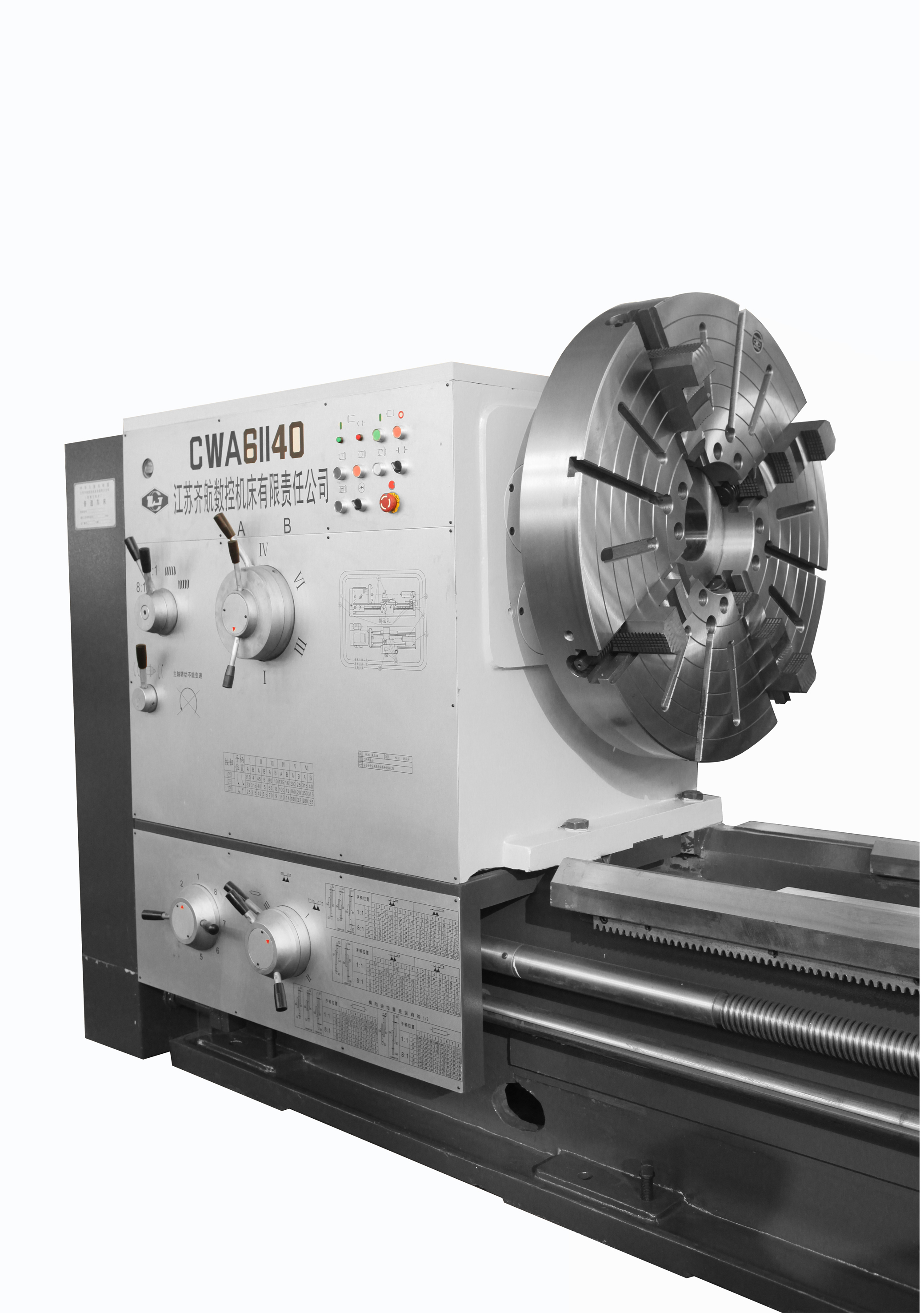
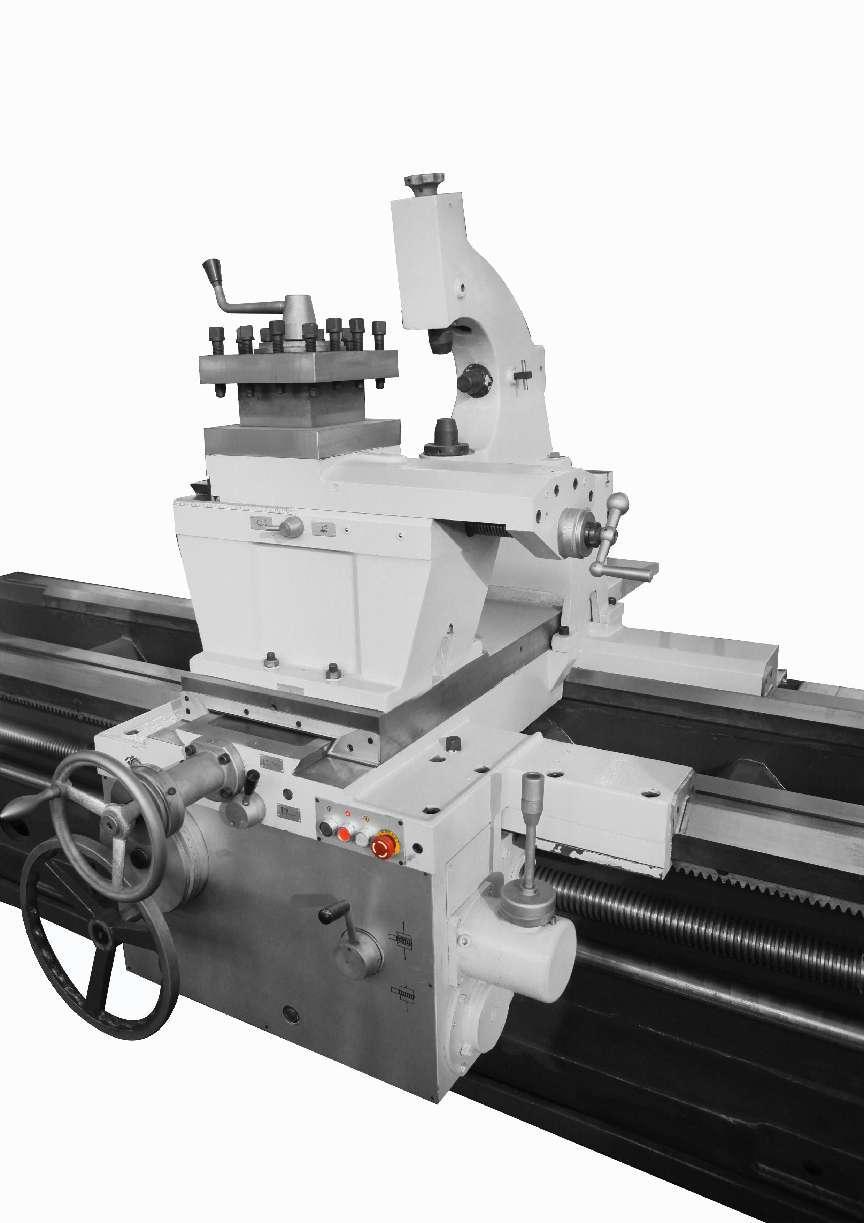
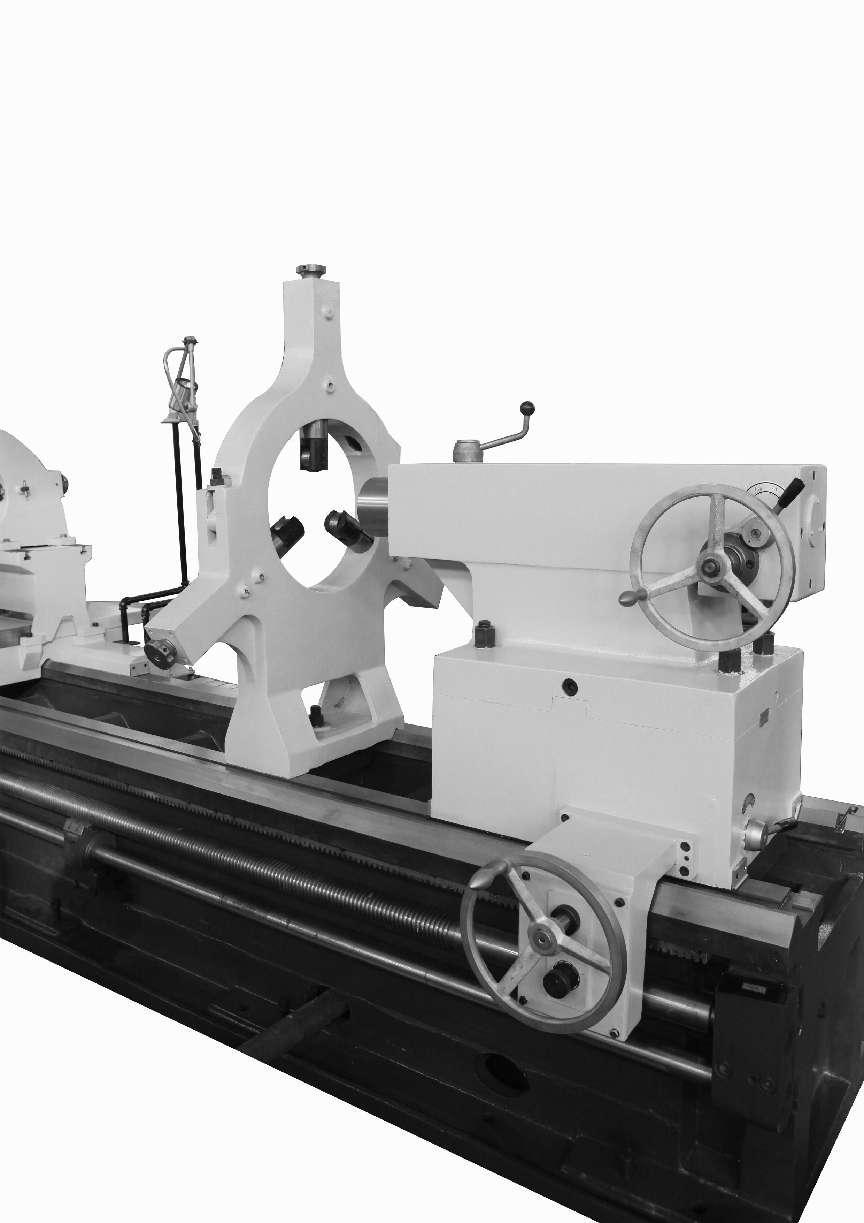
Bed: The main parts of the lathe machine are installed on the bed, so that they maintain an accurate relative position during work.The carriage and tailstock slide on a finely machined bed surface.
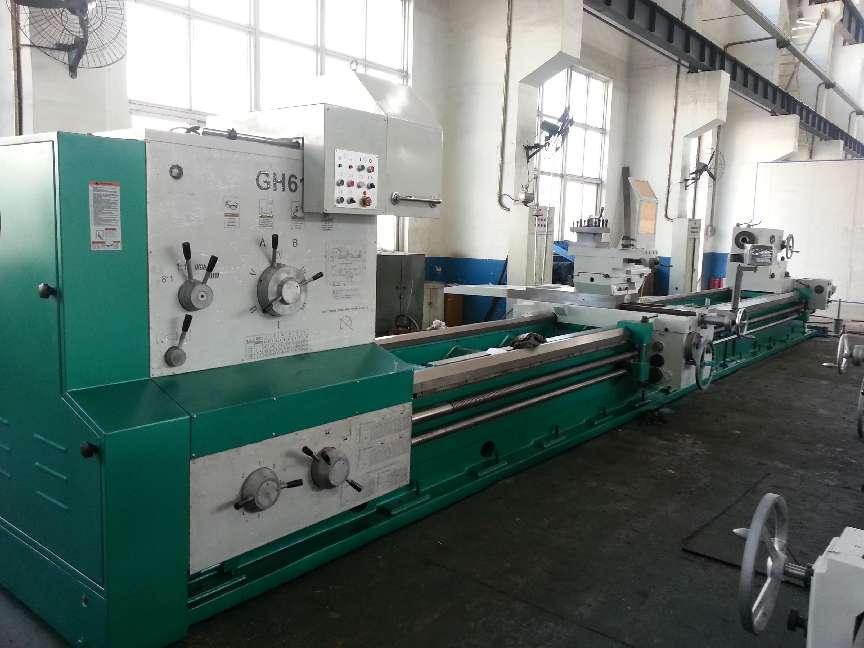
Headstock:The headstock is mounted rigidly to the bed and holds all the mechanisms, including various kinds and combinations of pulleys or gears.Its main task is to pass the rotational motion from the main motor through a series of speed change mechanisms so that the main shaft can obtain the required different speeds of forward and reverse rotations, and at the same time, the headstock splits part of the power to transmit the motion to the feed box.Headstock Medium spindle is a key part of the lathe.The smoothness of the spindle running on the bearing directly affects the processing quality of the workpiece. Once the rotation accuracy of the spindle is reduced, the use value of the machine tool will be reduced.
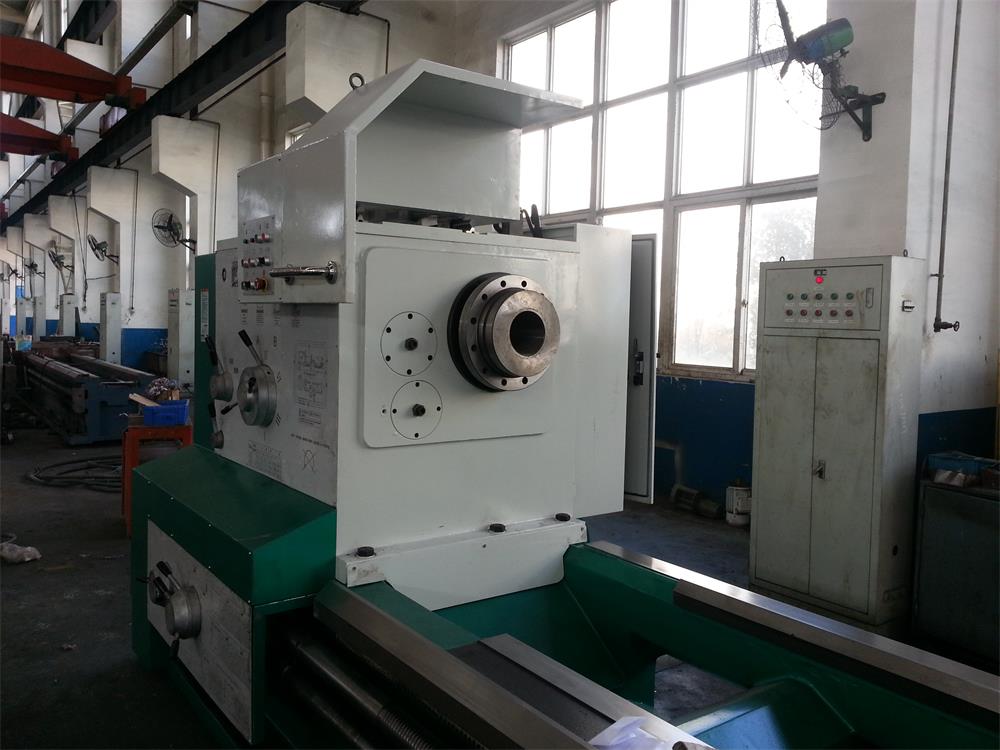
Feed box: The feed box is equipped with a speed change mechanism for feeding motion. Adjust the speed change mechanism to obtain the required feed amount or pitch, and transmit the motion to the tool holder through the smooth screw or lead screw for cutting.The lead screw is specially used for turning various threads. When turning other surfaces of the workpiece, only the smooth screw is used instead of the lead screw.
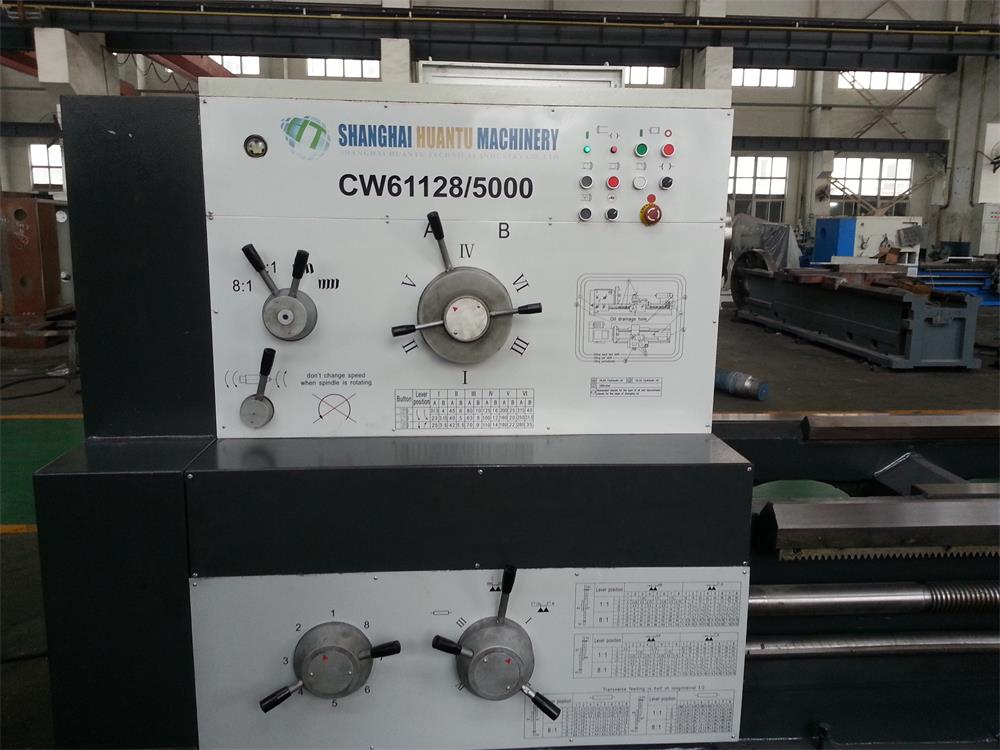
Tool holder: The tool holder is composed of several layers of tool posts. Its function is to clamp the tool and make the tool move longitudinally, laterally or obliquely.
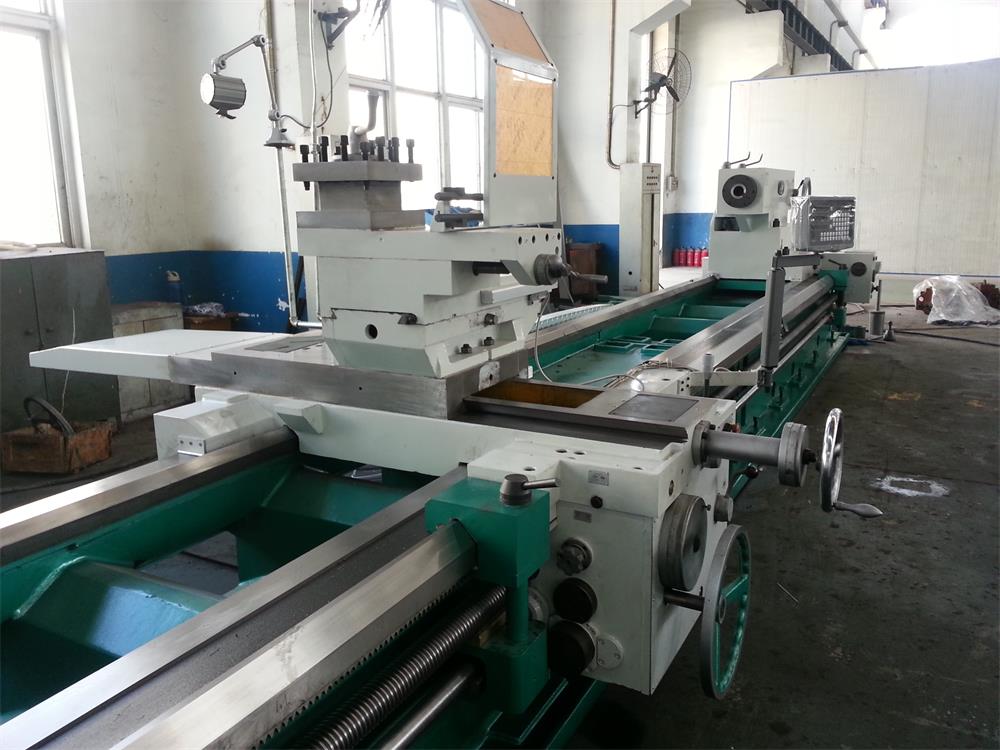
Tailstock: As a rear center for positioning support, it can also be installed with hole processing tools such as drills and reamers for hole processing.
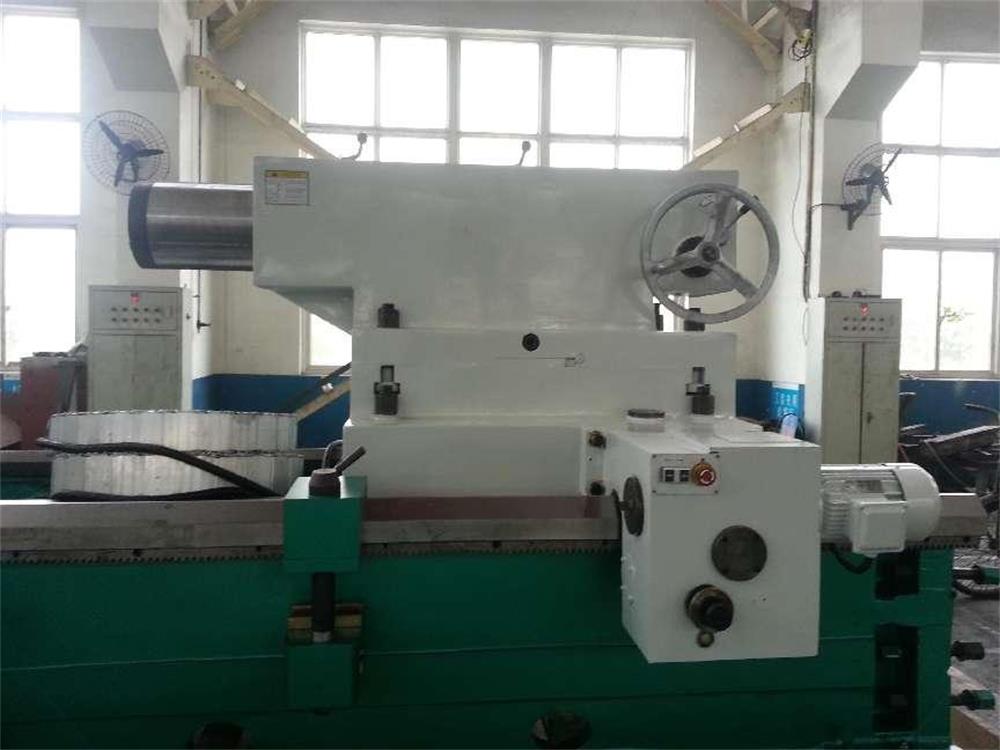
parts
Three-jaw chuck (for cylindrical workpieces)
four-jaw chuck (for irregular workpieces)
characteristic
Conventional machine tools have simple structure, easy operation, large spindle diameter, small footprint, large processing flexibility, easy maintenance, suitable for small batch processing and high cost performance.
The bed adopts an integral bed with high rigidity.The machine is equipped with a separate oil pump. The slide, tool holder, and saddle can move quickly. This machine tool can adopt GSK system or optional SIEMENS, FANUC numerical control system and other numerical control systems according to the user's requirements, which can perform high-speed, strong and stable cutting, high machining accuracy and simple programming.
The vertical and horizontal feed adopts AC servo motor, and the pulse encoder feedback is used as the feedback element. The vertical and horizontal motion guide rails are subjected to ultrasonic hardening and fine grinding treatment. The bed guide rail is pasted with PTFE soft tape, and the friction coefficient is small.
The main motor adopts the mixed speed regulation mode of magnetic regulation and voltage regulation, so as to make the spindle stepless speed regulation.
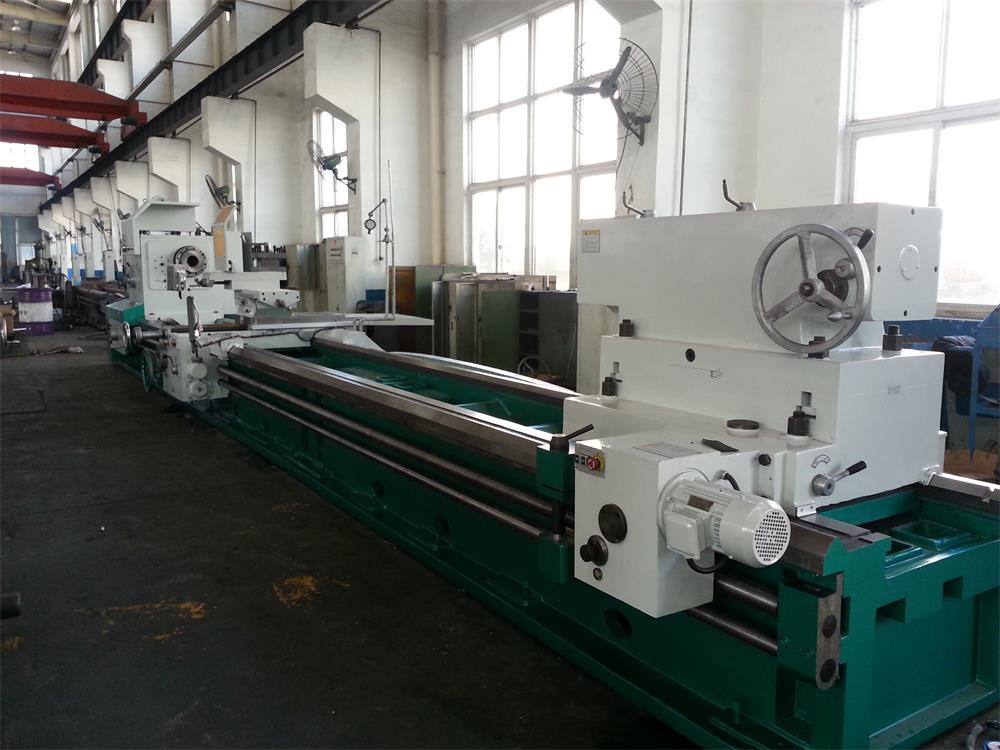
Operating procedures
1. Inspection before startup
1.1 Add appropriate grease according to the machine lubrication chart.
1.2 Check all electrical facilities, handle, transmission parts, protection and limit devices are complete, reliable and flexible.
1.3 Each gear should be at zero position, and the belt tension should meet the requirements.
1.4 It is not allowed to store metal objects directly on the bed, so as not to damage the bed.
1.5 The workpiece to be processed is free of mud and sand, preventing mud and sand from falling into the machine and wearing out the guide rail.
1.6 Before the workpiece is clamped, an empty car test operation must be carried out, and the workpiece can be loaded only after confirming that everything is normal.
2. Operation procedure
2.1 After the workpiece is installed, start the lubricating oil pump first to make the oil pressure meet the requirements of the machine tool before starting.
2.2 When adjusting the exchange gear rack, when adjusting the hanging wheel, the power supply must be cut off. After the adjustment, all bolts must be tightened, the wrench should be removed in time, and the workpiece should be disconnected for trial operation.
2.3 After loading and unloading the workpiece, the chuck wrench and floating parts of the workpiece should be removed immediately.
2.4 The tailstock, crank handle, etc. of the machine tool shall be adjusted to appropriate positions according to the processing needs, and shall be tightened or clamped.
2.5 Workpieces, tools and fixtures must be securely mounted. The floating force tool must extend the lead-in part into the workpiece before starting the machine tool.
2.6 When using the center rest or the tool rest, the center must be adjusted well, and there must be good lubrication and supporting contact surfaces.
2.7 When processing long materials, the protruding part behind the main shaft should not be too long.
2.8 When feeding the knife, the knife should approach the work slowly to avoid collision; the speed of the carriage should be uniform. When changing the tool, the tool and the workpiece must be kept at an appropriate distance.
2.9 The cutting tool must be tightened, and the extension length of the turning tool is generally not more than 2.5 times the thickness of the tool.
2.1.0 When machining eccentric parts, there must be proper counterweight to balance the center of gravity of the chuck, and the speed of the vehicle should be appropriate.
2.1.1. There must be protective measures for the workpiece whose chuck is beyond the fuselage.
2.1.2 The adjustment of the tool setting must be slow. When the tool tip is 40-60 mm away from the processing part of the workpiece, manual or working feed should be used instead, and rapid feed is not allowed to directly engage the tool.
2.1.3 When polishing the workpiece with a file, the tool holder should be retracted to a safe position, and the operator should face the chuck, with the right hand in front and the left hand behind. There is a keyway on the surface, and it is forbidden to use a file to process the workpiece with a square hole.
2.1.4 When polishing the outer circle of the workpiece with emery cloth, the operator should hold the two ends of the emery cloth with both hands to polish according to the posture specified in the previous article. It is forbidden to use your fingers to hold the abrasive cloth to polish the inner hole.
2.1.5 During automatic knife feeding, the small knife holder should be adjusted to be flush with the base to prevent the base from touching the chuck.
2.1.6 When cutting large and heavy workpieces or materials, sufficient machining allowance should be reserved.
3. Parking operation
3.1 Cut off the power and remove the workpiece.
3.2 The handles of each part are knocked down to the zero position, and the tools are counted and cleaned.
3.3 Check the condition of each protection device.
4. Precautions during operation
4.1 It is strictly forbidden for non-workers to operate the machine.
4.2 It is strictly forbidden to touch the tool, the rotating part of the machine tool or the rotating workpiece during operation.
4.3 It is not allowed to use emergency stop. In case of emergency, after using this button to stop, it should be checked again according to the regulations before starting the machine tool.
4.4 It is not allowed to step on the guide rail surface, screw rod, polished rod, etc. of the lathe. Except for the regulations, it is not allowed to operate the handle with feet instead of hands.
4.5 For parts with blisters, shrinkage holes or keyways on the inner wall, triangular scrapers are not allowed to cut the inner holes.
4.6 The compressed air or liquid pressure of the pneumatic rear hydraulic chuck must reach the specified value before it can be used.
4.7 When turning slender workpieces, when the protruding length of the front two sides of the head of the bed is more than 4 times the diameter, the center should be used according to the process regulations. Center rest or heel rest support. Guards and warning signs should be added when protruding behind the head of the bed.
4.8 When cutting brittle metals or cutting easily splashed (including grinding), protective baffles should be added, and operators should wear protective glasses.
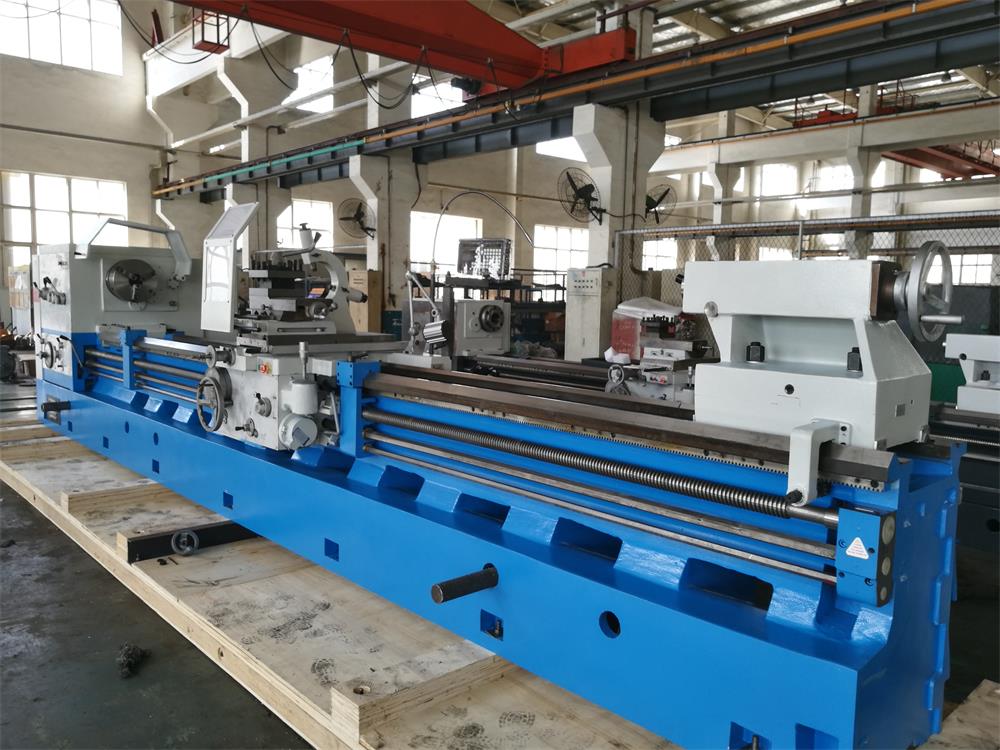
other
With the popularity of CNC machining,more and more automation equipment is emerging in the market.Traditional lathes have their own irreplaceable advantages and are still the necessary machines for most processing plants.
1. Conventional machine tools are more affordable
The purchase cost of CNC lathes is several times more expensive than that of conventional lathe with the same power, and the later maintenance, repair, supporting consumables and other costs are also much higher than it.
2.More suitable for small-scale machining
When only small batches of workpieces need to be machining,most skilled workers can machine the part with conventional machine tools with drawings of parts.
3.High salaries of CNC programmers and few talents
CNC programmers often require higher salaries, and there are many types of CNC systems. It is obviously more difficult to find an operator who is proficient in CNC machine tools than a conventional machine tool worker.
4.About business input costs
Considering the capital turnover of enterprises and the rational use of equipment, many enterprises keep manufacturing by conventional machine tools.
All in all, although CNC manufacturing has become a major trend in the development of the manufacturing industry, conventional machine tools still have their own unique advantages in the case of the popularization of intelligent equipment. With the continuous improvement of the intelligence of CNC machine tools in the future, traditional machine tools may be replaced on a large scale, but it is not feasible to completely eliminate them.
MODEL | CW61(2)63E | CW61(2)80E | CW61(2)100E | CW61(2)120E | CWA61100 |
CAPACITIES | |||||
Max.swing over bed | 630mm | 800mm | 1000mm | 1200mm | 1000mm |
Max.swing over cross slide | 350mm | 485mm | 685mm | 800mm | 620mm |
Max.turning length | 750,1250,1750,2750,3750,4750,5750,7750,9750,11750mm | 1.5m 2m 3m 4m 5m 6m 8m 10m 12m | |||
Max.swing over gap | 830mm | 1000mm | 1200mm | 1400mm | 780mm |
Valid length of gap | 230m | 8T | |||
Bed width | 550mm | ||||
HEAD-STOCK | Φ130mm | ||||
Spindle hole | 105mm OR 130mm (OPTIONAL FOR CW6180E+) | Metric 140# | |||
Spindle nose | D-11 or C-11 | 3.15-315r/min or 2.5-250r/min | |||
Spindle taper | Φ120mm taper1:20(Φ140, OPTIONAL FOR CW6180+) | Forward 21kinds,Reversal 12kinds | |||
Spindle speeds(Number) | 14-750RPM(18 STEPS) | ||||
GEAR BOX-THREADS & FEEDS | 44kinds 1-120mm | ||||
Metric threads range(kinds) | 1-240mm(54 kinds) | 31kinds 1/4-24 T/I | |||
Inch threads rangs(Kinds) | 28-1 inch(36 kinds) | 45kinds 0.5-60mm | |||
Moudle threads range(kinds) | 0.5-60 DP(27 kinds) | 38kinds 1/2-56DP | |||
Diametral threads range(kinds) | 30-1 t.p.i.(27 kinds) | 56kinds 0.1-12mm | |||
Longtudinal feeds range(kinds) | 0.048-24.3mm/r (72 kinds) | 56kinds 0.05-6mm | |||
Cross feed range(kinds) | 0.024-12.15mm/r (72 kinds) | 3400mm/min,1700mm/min | |||
Rapid feed:Long./Cross | 4/2m/min | ||||
Leadscrew size:Diameter/Pitch | T48mm/12mm OR T55mm/12mm(for 5M+) | 48mm | |||
CARRIAGE | 45*45mm | ||||
Cross slide travel | 350mm | 420mm | 520mm | ||
Compound rest travel | 200mm | 650mm | |||
Size of tool shank | 32*32mm | 280mm | |||
TAILSTOCK | |||||
Spindle diameter | 100mm | 120mm | Φ160mm | ||
Spindle taper | MORSE #6 | Metric 80# | |||
Spindle travel | 240mm | 300mm | |||
MOTOR | |||||
Main drive motor | 11kw | 22kw | |||
Coolant pump motor | 0.09kw | 0.15kw | |||
Rapid feed motor | 1.1kw | 1.5kw |
Post time: Apr-14-2022