High-speed CNC Vertical Machining Center CL Series
Features
CL series vertical machining centers are mainly used for large, medium and small batch processing and production of various types of product parts, accessories, etc. For example, they provide users with high-speed parts processing solutions in the fields of automobile industry, military industry, aerospace, etc.
High-speed CNC vertical machining center has the characteristics of high rigidity, high precision and high efficiency processing. The column adopts a herringbone design with a large span, which can greatly enhance the bending and torsion strength of the column; the worktable adopts a reasonable slider span and is surface quenched to make the worktable evenly stressed and improve the hardness; the bed adopts a trapezoidal cross-section to reduce the the center of gravity improves torsional strength; the entire machine uses finite element analysis to design each component to provide the best overall stability.
The three-axis rapid feed is 48M/min, the T-T tool change time is only 4 seconds, the tool magazine is fully loaded 24 of tools, tool change without alarm, and the 3-dimensional inspection of each machine's trial processing sample has passed, ensuring the high efficiency, continuous stability of the machine tool after leaving the factory. It is suitable for various two- and three-dimensional concave and convex models with complex shapes and complex cavities and surfaces. It is also suitable for milling, drilling, expanding and boring of valves, cams, molds, plates and boxes in the manufacturing industry. Tapping and other processing processes are more suitable for both small and medium-sized batches of multi-variety processing and production, and can also be entered into automatic lines for mass production.
Adopting C80 PLus system, 15-inch large LCD display, dynamic graphic display of tool path, intelligent warning display, self-diagnosis and other functions make the use and maintenance of machine tools more convenient and faster; the high-speed bus communication method greatly improves the CNC system The data processing capability and control performance are improved, the program storage capacity is increased to 4G, and the pre-reading capability is increased to 3000 lines/second, which facilitates the fast and efficient transmission and online processing of large-capacity programs.
Technical Specifications
Item |
CL700 |
CL800 |
CL1000 |
CL1300 |
CL1500 |
|
Travel |
X/Y/Z axis travel |
700/400450mm |
800/600/500mm |
1000/600/500mm |
1300/700/650mm |
1500/800/700mm |
Distance from spindle end face to worktable center |
120-570mm |
120-620mm |
120-620mm |
120-770mm |
170-870mm |
|
Workable |
Workable size |
850*400mm |
900*500mm |
1100*500mm |
1500*700mm |
1700*800mm |
Max.load of worktable |
350kg |
500kg |
600kg |
900kg |
1500kg |
|
Spindle | Spindle specifications (installation diameter/drive mode) |
140mm/Direct type |
150mm,Direct type |
|||
Spindle taper hole |
BT40 |
|||||
Max.spindle speed |
12000rpm |
|||||
Spindle motor power |
55-11kw |
7.5-15KW |
7.5-15KW |
7.5-15KW |
11-22RW |
|
Spindle motor torque |
35=70Nm |
48-96Nm |
48-96Nm |
48-96Nm |
70-140Nm |
|
Feed rate | Rapid moving speed |
48/48/4&mm |
30/30/24mm |
24/24/20mm |
||
Cutting feed |
1=12m/nin |
1=10m/min |
1=10my/min |
|||
Tool magazine | Tool magazine capacity |
24tools |
||||
Max. tool length |
300mm |
|||||
Max. tool diameter |
125mm |
|||||
Max. tool weight |
8kg/t |
|||||
Tool change time, (tool to tool) |
1.55 sec |
|||||
Three axis | X-axis guide rail (linear guide width, number of sliders) |
30mm/2 |
35mm/2 |
35mmy2 |
45mmy3 |
45mmB |
Y-axis guide rail (linear guide width, number of sliders) |
30mmy2 |
35mm/2 |
35mmy2 |
45mmy4 |
45mm/2 |
|
Z-axis guide rail (linear guide width, number of sliders) |
35mm/2 |
35mm/2 |
35mmy2 |
45mmy3 |
55mmy3 |
|
X-axis screw |
Φ28x16 |
Φ36*16 |
Φ36×16 |
Φ40x10 |
Φ50x10 |
|
Y-axis screw |
Φ28*16 |
Φ36*16 |
Φ36×16 |
Φ40*10 |
Φ50x10 |
|
Z-axis screw |
Φ32×16 |
Φ36*16 |
Φ36*16 |
Φ40x10 |
Φ50x10 |
|
Accuracy | Positioning Accuracy |
±0.005/300mm |
||||
Repeatability |
±0.003mm |
|||||
Required power source |
Electricity demand |
Three-phase 20V±10%,50Hz±1% |
||||
Air pressure demand |
≥6kg/cm² |
|||||
Air source demand |
≥0.5mm³/min |
|||||
Machine size | Machine weight |
3500kg |
5500kg |
6000kg |
8000kg |
9000kg |
Machine size |
2253×2494×2506 |
2453×3122×2635 |
2653×3122×2635 |
3565×3008×2714 |
3700×2772×2764 |
Configuration Introduction
(1)BT40 Spindle
BT40 spindle with high speed, high efficiency, high torque processing characteristics, to meet the processing needs of a variety of typical materials.
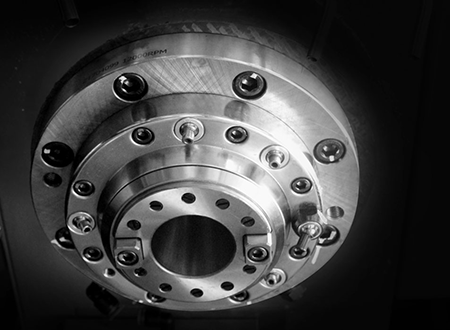
(2)Siemens system
With the latest Siemens systems which has intuitive and precise panel, easy to operate.

(3)High rigid Machine Bed
Finite element analysis design is used to perfect the large casting bed body, column, saddle, bracket and workbench parts to provide optimal rigidity and torsional rigidity.
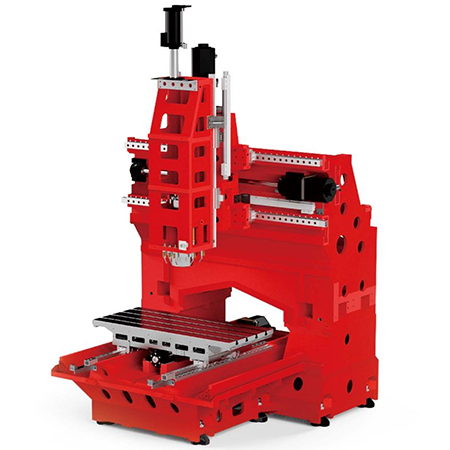
(4)Oil-water Separator
Oil-water separation and recovery of floating oil for machine tool coolant (cutting fluid), with recovery capacity of 98%.
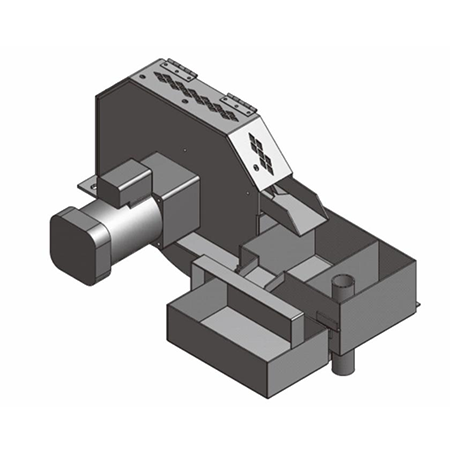
Processing Cases
Automotive Industry
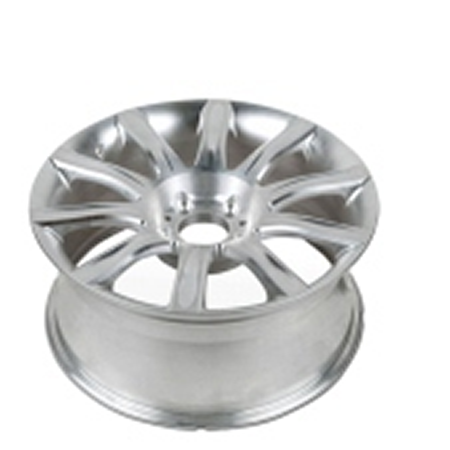
Wheel hub
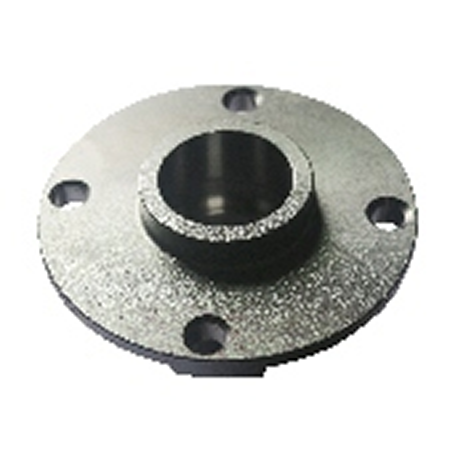
Hub flange
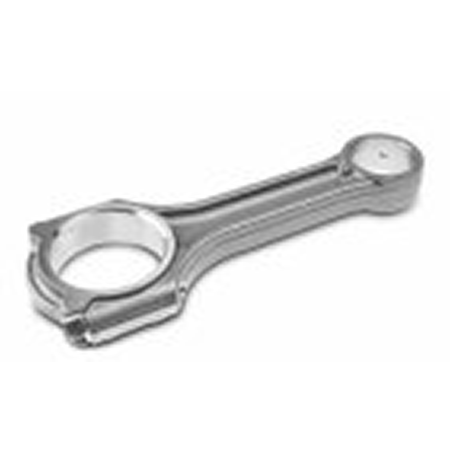
Connecting rod
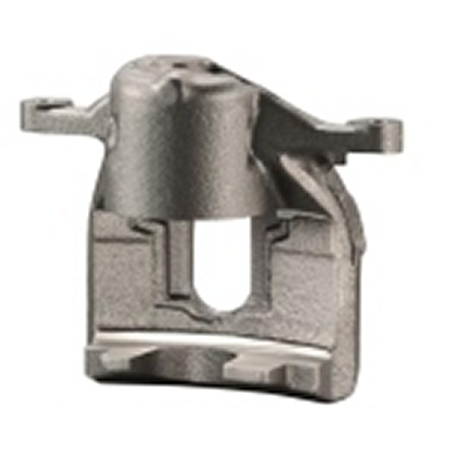
Brake caliper cylinder
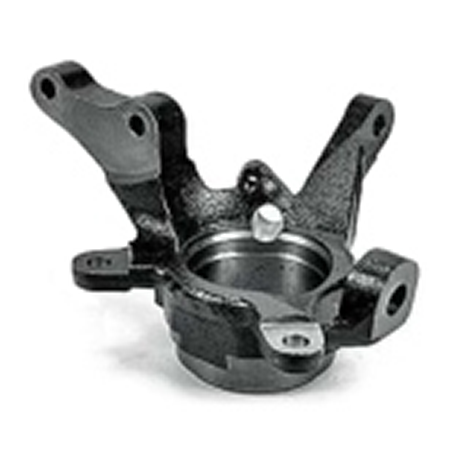
Automobile steering knuckle
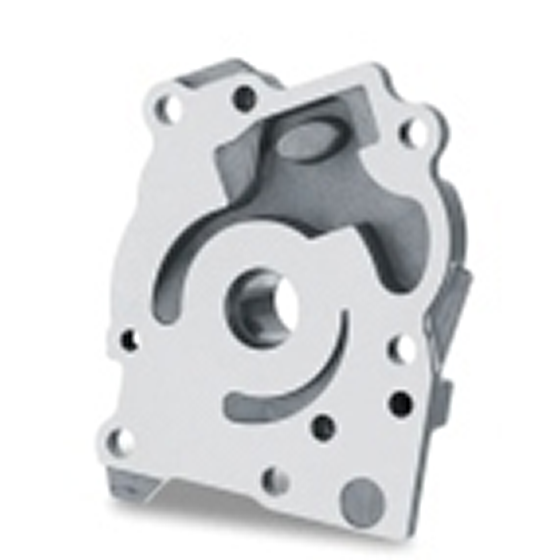
Pump case
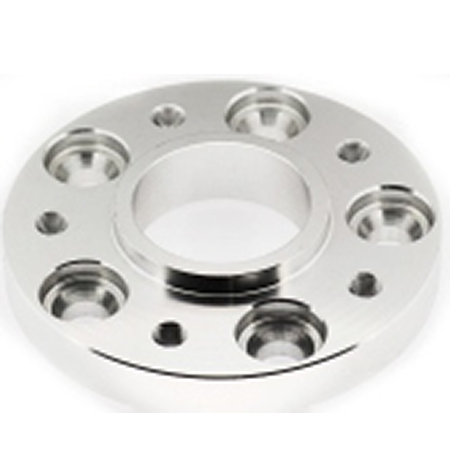
Flange
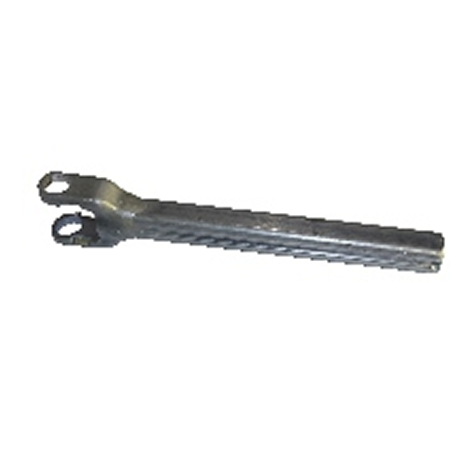
Universal joint
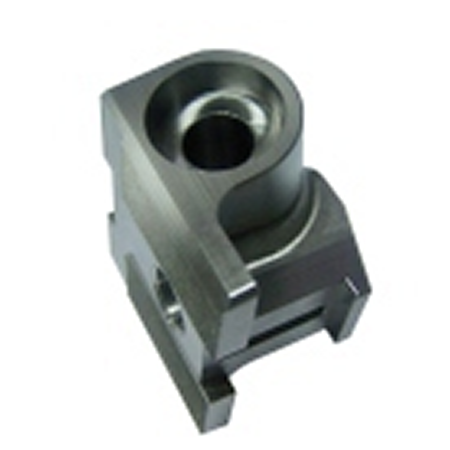
Bearing holder
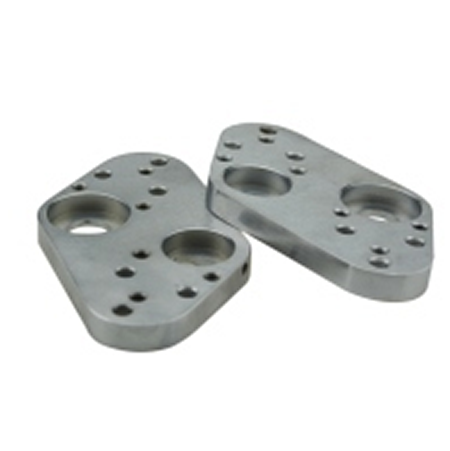
Land
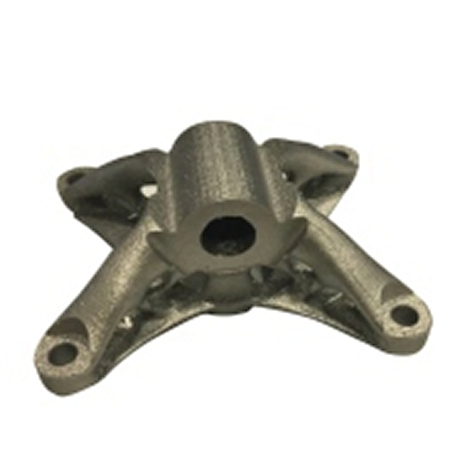
Suspension damper
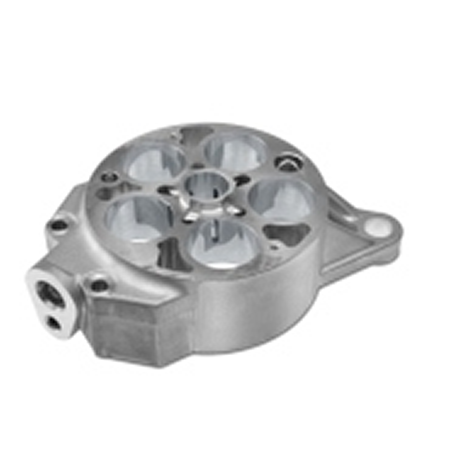
Rear cylinder
Precision Fixtures
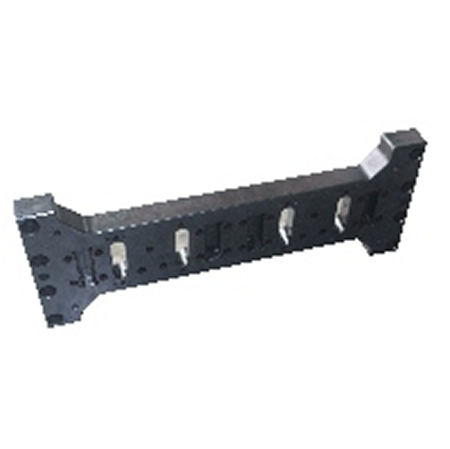
Fixture bottom plate
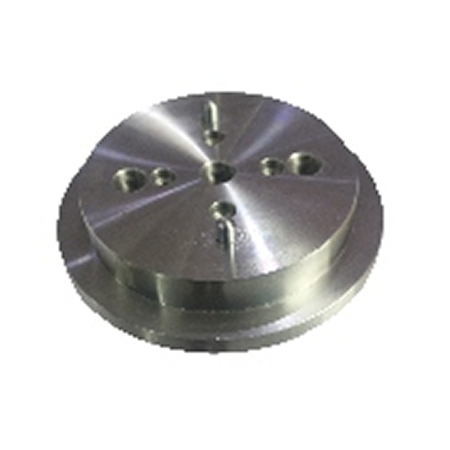
Fixture chuck
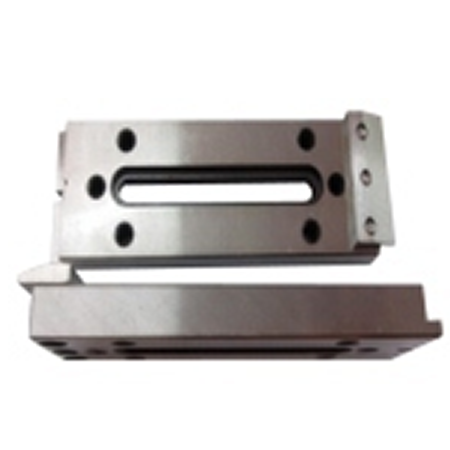
Fixture accessories
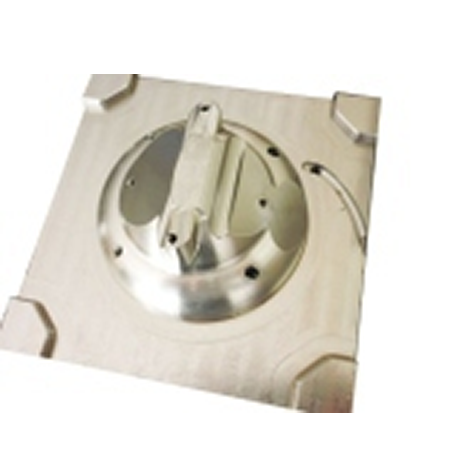
Injection mold
Military Industry
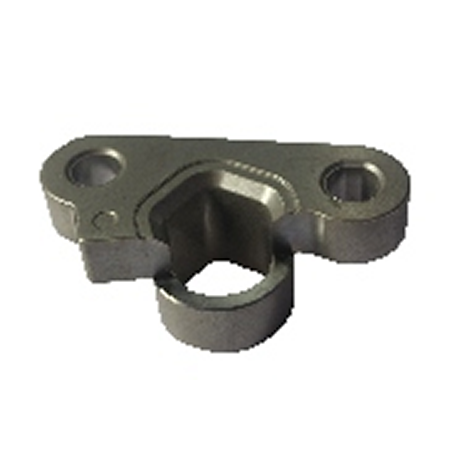
Powder metallurgy products
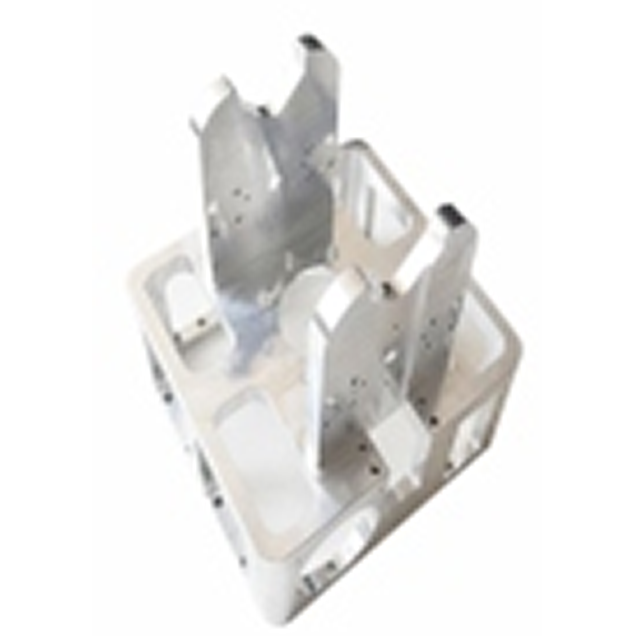
Aero seat frame
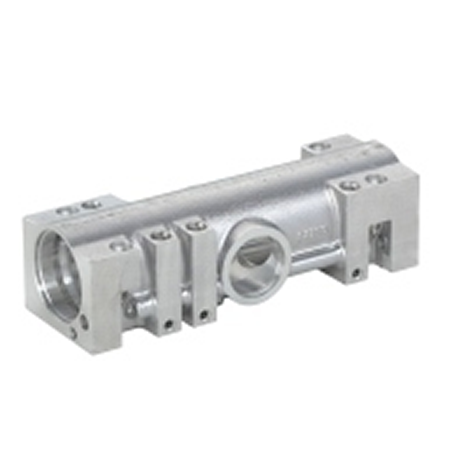
Door closers housing
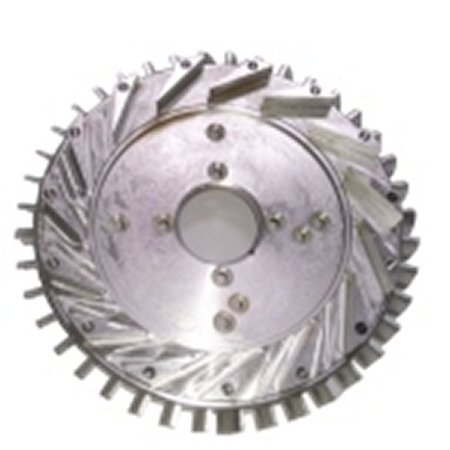
Aviation amplifier