5-Axis Vertical Machining Center CV Series
Features
Machine introduction
The five-axis vertical machining center CV series has the characteristics of high rigidity, high precision and high efficiency machining. The column adopts a herringbone design with a large span, which can greatly enhance the bending and torsional strength of the column; the workbench adopts a reasonable slider span and is surface quenched, so that the force on the workbench is uniform and the hardness is improved; the bed adopts a trapezoidal cross-section, reducing The center of gravity improves the torsional strength; the whole machine uses finite element analysis to design each component to provide the best overall stability.
The fastest three-axis rapid displacement can reach 48M/min, the T-T tool change time is only 2.5S, the tool magazine is fully loaded for 24t. It is suitable for various 2D and 3D concave-convex models with complex shapes and complex cavities and surfaces. It is also suitable for milling, drilling, expanding, boring, Tapping and other processing procedures are more suitable for both small and medium-sized batches of multi-variety processing and production, and can also be used in automatic lines for mass production.
The dynamic graphic display of the tool track, intelligent warning display, self-diagnosis and other functions make the use and maintenance of the machine tool more convenient and fast; The reading capacity is increased to 3000 lines/second, which facilitates the fast and efficient transmission and online processing of large-capacity programs.
The RTCP (Rotation Tool center Point) of the five-axis machining center is the tool tip point control function. After turning on the RTCP function, the controller will change from originally controlling the end face of the tool holder to controlling the tool tip point. The tool tip following can compensate for the linearity caused by the rotary axis. Error to prevent Tool collision. At point A of the workpiece, the centerline of the tool axis changes directly from the horizontal position to the vertical position. If the linear error is not corrected, the tool tip will deviate from point A or even penetrate the workpiece, causing a serious accident. Because the continuous movement of the swing axis and the rotary axis causes changes in the position of point A, the original tool tip position in the program must be corrected to ensure that the tool tip position coordinates are always unchanged relative to point A, as if the tool tip is moving with point A. , this is the tip of the Tool following.
This function has 0 ~ 9 levels, the 9th level is the highest precision,while the 1st - 8th level compensates the servo backward error, and gives the processing path proper smoothness.
High-speed and High-precision Three-dimensional Processing
The high-speed spindle, the 3D arc machining control can pre-read 2000blocks and smooth path correction for high-speed and high-precision machining.
High Rigidity Structure
Improve the form of structure and optimize the allocation to enhance the machine's rigidity. The shape of machine tool and column and the allocation optimization are the most suitable shape through CAE analysis. The various improved measures which are invisible outside are reflecting a stable cutting ability which the spindle speed cannot show.
Technical Specifications
Item |
unit |
CV200 |
CV300 |
CV500 |
|
Travel
|
X/Y/Z axis travel |
mm |
500×400×330 |
700*600*500 |
700×600×500 |
Distance from spindle end face to worktable surface |
mm |
100-430 |
150-650 |
130-630 |
|
Distance from spindle center to column guide rail surface |
mm |
412 |
628 |
628 |
|
The maximum distance between the A-axis 90° spindle center and the C-axis disk surface |
mm |
235 |
360 |
310 |
|
3 axis feed
|
X/Y/Z axis rapid displacement |
m/min |
48/48/48 |
48/48/48 |
36/36/36 |
Cutting feed rate |
mm/min |
1-24000 |
1-24000 |
1-24000 |
|
Spindle
|
Spindle specifications (installation diameter/transmission mode) |
mm |
95/direct |
140/Direct |
140/Direct |
Spindle taper |
mm |
BT30 |
BT40 |
BT40 |
|
Spindle speed |
r/min |
12000 |
12000 |
12000 |
|
Spindle motor power (continuous/S3 25%) |
kW |
8.2/12 |
15/22.5 |
15/22.5 |
|
Spindle Motor Torque (Continuous/S3 25%) |
N.m |
26/38 |
47.8/71.7 |
47.8/71.7 |
|
Tool magazine
|
Magazine capacity |
T |
21T |
24T |
24T |
Tool change time (T-T) |
s |
2.5 |
4 |
4 |
|
Max.Tool diameter(full tool/empty tool) |
mm |
80 |
70/120 |
70/120 |
|
Max.Tool length |
mm |
250 |
300 |
300 |
|
Max. Tool weight |
kg |
3 |
8 |
8 |
|
Guide
|
X-axis guide (size/number of sliders) |
mm |
30/2 |
35/2 roller |
45/2 roller |
Y-axis guide (dimensions/quantity of sliders) |
|
30/2 |
35/2 roller |
45/2 roller |
|
Z-axis guide (dimensions/quantity of sliders) |
|
30/2 |
35/2 roller |
45/2 roller |
|
Screw
|
X-axis screw |
|
Φ28×16 |
Φ40×16 |
Φ40×16 |
Y-axis screw |
|
Φ28×16 |
Φ40×16 |
Φ40×16 |
|
Z axis screw |
|
Φ32×16 |
Φ40×16 |
Φ40×16 |
|
Accuracy
|
Positioning accuracy |
mm |
±0.005/300 |
±0.005/300 |
±0.005/300 |
Repeatability |
mm |
±0.003/300 |
±0.003/300 |
±0.003/300 |
|
5 axis
|
Turntable drive method |
|
Moter direct |
Roller cam |
roller cam |
Turntable diameter |
mm |
Φ200 |
Φ300*250 |
φ500*400 |
|
Allowable load weight of turntable (in horizontal/inclined) |
kg |
40/20 |
100/70 |
200 |
|
A/C-axis max. speed |
rpm |
100/230 |
60/60 |
60/60 |
|
A-axis positioning/repeatability |
arc-sec |
10/6 |
15/10 |
15/10 |
|
C-axis positioning/repeatability |
arc-sec |
8/4 |
15/10 |
15/10 |
|
Lubrication
|
Lubrication unit capacity |
L |
1.8 |
1.8 |
1.8 |
Oil separator type |
|
volumetric |
Grease lubrication |
volumetric |
|
Others
|
Air demand |
kg/c㎡ |
≥6 |
≥6 |
≥6 |
Air source flow |
mm3/min |
≥0.2 |
≥0.4 |
≥0.4 |
|
battery capacity |
KVA |
10 |
22.5 |
26 |
|
Machine Weight (Comprehensive) |
t |
2.9 |
7 |
8 |
|
Mechanical Dimensions (L×W×H) |
mm |
1554×2346×2768 |
2248*2884*2860 |
2610×2884×3303 |
Processing Example
1.Automotive Industry
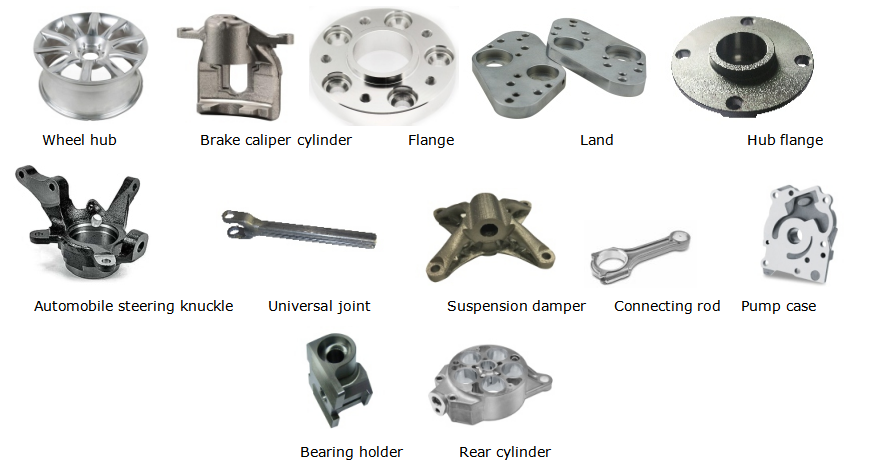
2.Precision fixture

3.Military industry
