Five-axis Vertical Machining Center CBS Series
Features
1.Main performance advantages
1.1.The X-axis adopts direct drive technology, the Y-axis adopts parallel direct drive technology and synchronous control, with high thrust, low noise, fast response speed, and excellent dynamic performance. The three-axis of X/Y/Z all adopt high-precision linear grating feedback, with high positioning accuracy
1.2.The high-torque torque motor drives the A-axis and C-axis to rotate, with zero transmission chain, zero backlash, and good rigidity; the high-precision angle encoder achieves precise positioning
1.3.The spindle adopts a high-speed electric spindle structure with high speed and low noise.
2.High-rigidity bridge structure
2.1.The CBS series adopts a bridge structure layout, and X/Y/Z achieves constant motion, which is not affected by the weight of the A/C axis.
2.2.The A/C axis operates independently, and the weight of the workpiece does not affect the other three axis.
2.3.The gantry structure and the swing and rotary table supported at both ends can maintain high-precision processing for a long time.
3.Efficient turning function
4.High-speed and high-rigidity rotary table realizes efficient milling and turning composite processing
The precision five-axis rotary table directly driven by the torque motor is used in CNC machine tools and can perform five-axis simultaneous processing. It has the advantages of high speed, high precision, stability and reliability, and easy operation.
5.Maintaining high-precision machining spindles
Mastering core technologies and independently developing spindles
Oturn has mastered core technologies and has the ability to design, manufacture and assemble spindles. With a 1000m2 constant temperature workshop and a sophisticated modular production model, Oturn spindles have the characteristics of high rigidity, high speed, high power, high torque and high reliability.
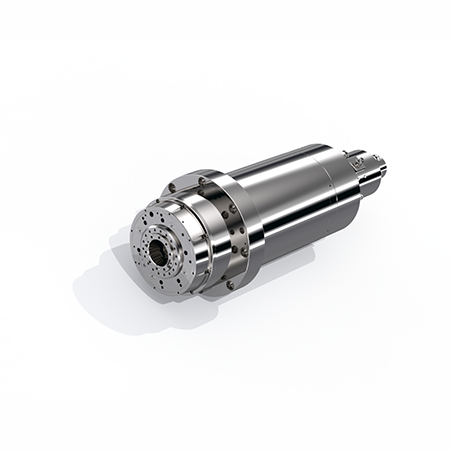
The independently developed HSKE40/HSKA63/HSKA100 built-in spindle is adopted. Within the spindle rotation range, the vibration and vibration are eliminated to achieve stable accuracy in high-speed and long-term processing. The spindle uses forced cooling to cool the motor and front and rear bearings.
6.Built-in motor structure
By eliminating the drive gear, vibration during high-speed rotation can be minimized, thereby improving the accuracy of the machined surface and extending the life of the tool.
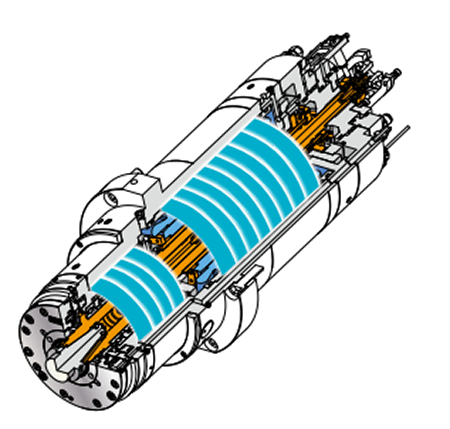
7.Spindle temperature management
By circulating the temperature-controlled cooling oil, the thermal displacement of the spindle caused by the heat generated by each component can be suppressed, thereby preventing changes in machining accuracy.
8.Leading the world in linear motors
Linear motors
8.1.Equipped with linear motor drive, there is no mechanical contact during movement, no mechanical loss, no backlash transmission, and fast response speed.
8.2.Absolute optical scale for full closed-loop control.
Absolute grating ruler, nanometer-level detection accuracy, resolution up to 0.05μm, to achieve full closed-loop control.
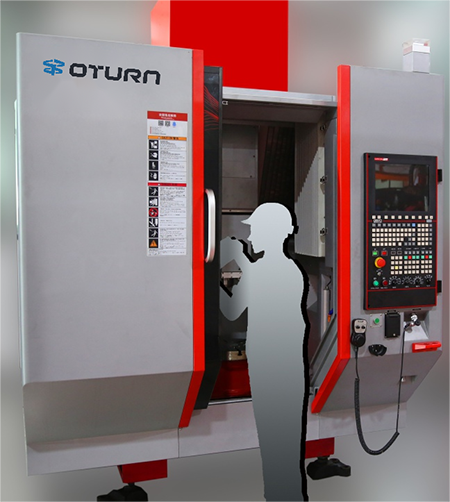
9.Excellent ergonomic design
Based on ergonomic design, it is easy for operators to use and improves operability and maintainability.
9.1.Excellent accessibility
In order to improve the performance of accessing the workbench, the cover at the bottom of the operation door is retreated to the side of the workbench to ensure sufficient working space.
9.2.Large window for easy observation of processing
The large window makes it easy to observe the processing status of the workpiece. In particular, frequent confirmation of cutting conditions and changes in operations during adjustment operations can also be easily completed, improving work efficiency.
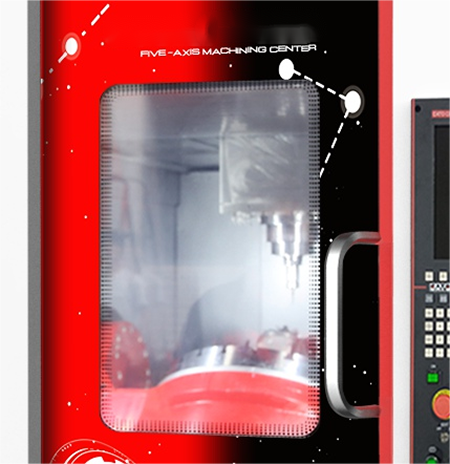
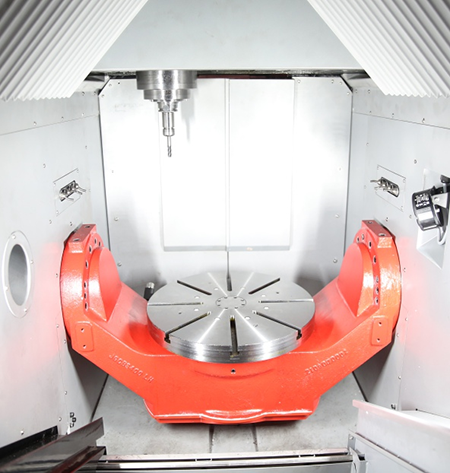
9.3.Centralized configuration of maintenance units
In order to improve the performance of accessing the workbench, the cover at the bottom of the operation door is retreated to the side of the workbench to ensure sufficient working space.
9.4.Wide operation door for easy access by crane
When performing operations such as workpiece replacement, the workload of personnel can be reduced, and at the same time, there is sufficient operating space when using a crane.
9.5.Pleasant and friendly operation panel
The rotatable operation panel that conforms to the height of the human body allows the operator to operate and program the machine in a comfortable posture.
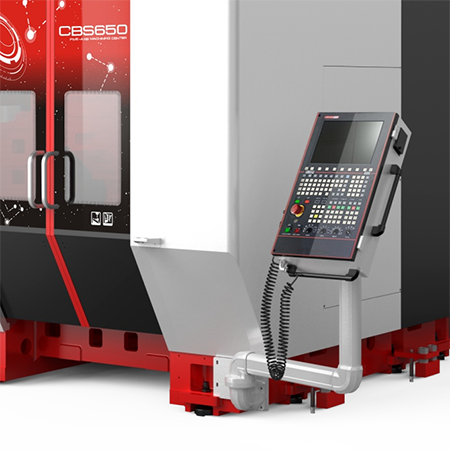
Technical Specifications
Item |
CBS200 |
CBS200C |
CBS300 |
CBS300C |
CBS400 |
CBS400C |
|
Travel |
X/Y/Z axis travel |
300*350*250 |
300*350*250 |
460*390*400 |
|||
Distance from spindle face to worktable center |
130-380 |
130-380 |
155-555 |
||||
Spindle |
Spindle taper |
E40 |
E40 |
E40 |
|||
Max.spindle speed |
30000 |
30000 |
30000 |
||||
Spindle motor power (continuous/S325%) |
11/13.2 |
11/13.2 |
11/13.2 |
||||
Spindle motor torque (continuous/S325%) |
11.5/13.8 |
11.5/13.8 |
11.5/13.8 |
||||
Feed |
Rapid speed of X/Y/Z axis (m/min)
|
48/48/48 |
48/48/48 |
30/30/30 |
|||
Cutting feed(mm/min) |
1-24000 |
1-24000 |
1-12000 |
||||
Rotary table |
Rotary table diameter |
200 |
300 |
400 |
|||
Allowable load weight |
30 |
20 |
40 |
25 |
250 |
100 |
|
A-axis tilting angle |
±110° |
±110° |
±110° |
||||
C-axis rotation |
360° |
360° |
360° |
||||
A-axis rated/max.speed |
47/70 |
47/70 |
30/60 |
||||
A-axis Rated/max.torque |
782/1540 |
782/1540 |
940/2000 |
||||
C-axis rated/max.speed |
200/250 |
1500/2000 |
200/250 |
1500/2000 |
100/150 |
800/1500 |
|
C-axis rated/max.torque |
92/218 |
15/30 |
92/218 |
15/30 |
185/318 |
42/60 |
|
A-axis positioning accuracy/repeatability |
10/6 |
10/6 |
10/6 |
||||
C-axis positioning accuracy/repeatability |
8/4 |
8/4 |
8/4 |
||||
ATC |
Tool magazine capacity |
16 |
16 |
26 |
|||
Tool max. diameter/ length |
80/200 |
80/200 |
80/200 |
||||
Max.tool weight |
3 |
3 |
3 |
||||
Tool change time (tool to tool) |
4 |
4 |
4 |
||||
Three- axis |
X-axis guide (linear guide width/ number of sliders) |
30/2 |
30/2 |
35/2 |
|||
X-axis guide (linear guide width/ number of sliders) |
35/2+30/2 |
35/2+30/2 |
45/2 |
||||
Z-axis guide (linear guide width/ number of sliders) |
25/2 |
25/2 |
35/2 |
||||
X-axis linear motor power (continuous/max.) |
1097/2750 |
1097/2750 |
φ40×10 (screw) |
||||
Y-axis linear motor power (continuous/max.) |
3250/8250 |
3250/8250 |
|
||||
Z-axis linear motor power (continuous/max.) |
1033/1511 |
1033/1511 |
|
||||
Accuracy |
Positioning accuracy |
0.005/300 |
0.005/300 |
0.005/300 |
|||
Repeatability |
0.003/300 |
0.003/300 |
0.003/300 |
||||
Power source |
Power supply capacity |
25 |
30 |
25 |
30 |
30 |
35 |
Air pressure |
≥0.6Mpa ≥400L/min |
≥0.6Mpa ≥400L/min |
≥0.6Mpa ≥400L/min |
||||
Machine size |
Machine size |
1920*3030*2360 |
1920*3030*2360 |
2000*2910*2850 |
|||
Machine size (including chip conveyor and other peripheral equipment) |
3580*3030*2360 |
3580*3030*2360 |
3360*2910*2850 |
||||
Weight |
4.8T |
4.8T |
5T |
Item |
CBS500 |
CBS500C |
CBS650 |
CBS650C |
CBS800 |
CBS800C |
|
Travel |
X/Y/Z axis travel |
500*600*450 |
650*800*560 |
800*910*560 |
|||
Distance from spindle face to worktable center |
130-580 |
110-670 |
100-660 |
||||
Spindle |
Spindle taper |
A63 |
A63 |
A63 |
|||
Max.spindle speed |
20000 |
20000 |
20000 |
||||
Spindle motor power (continuous/S325%) |
30/34 |
30/34 |
30/34 |
||||
Spindle motor torque (continuous/S325%) |
47.7/57.3 |
47.7/57.3 |
47.7157.3 |
||||
Feed |
Rapid speed of X/Y/Z axis (m/min)
|
48/48/48 |
48/48/48 |
48/48/48 |
|||
Cutting feed(mm/min) |
1-24000 |
1-24000 |
1-24000 |
||||
Rotary table |
Rotary table diameter |
500 |
650 |
800 |
|||
Allowable load weight |
600 |
240 |
800 |
400 |
1000 |
400 |
|
A-axis tilting angle |
±110° |
±110° |
±110° |
||||
C-axis rotation |
360° |
360° |
360° |
||||
A-axis rated/max.speed |
60/80 |
40/8C |
40/80 |
||||
A-axis Rated/max.torque |
1500/4500 |
3500/7000 |
3500/7000 |
||||
C-axis rated/max.speed |
80/120 |
600/1000 |
50/80 |
450/800 |
50/80 |
450/800 |
|
C-axis rated/max.torque |
355/685 |
160/240 |
964/1690 |
450/900 |
964/1690 |
450/900 |
|
A-axis positioning accuracy/repeatability |
10/6 |
10/6 |
10/6 |
||||
C-axis positioning accuracy/repeatability |
8/4 |
8/4 |
8/4 |
||||
ATC |
Tool magazine capacity |
25 |
30 |
30 |
|||
Tool max. diameter/ length |
80/300 |
80/300 |
80/300 |
||||
Max.tool weight |
8 |
8 |
8 |
||||
Tool change time (tool to tool) |
4 |
4 |
4 |
||||
Three- axis |
X-axis guide (linear guide width/ number of sliders) |
35/2 |
45/2 |
45/2 |
|||
X-axis guide (linear guide width/ number of sliders) |
45/2 |
45/2 |
45/2 |
||||
Z-axis guide (linear guide width/ number of sliders) |
35/2 |
35/2 |
35/2 |
||||
X-axis linear motor power (continuous/max.) |
2167/5500 |
3250/8250 |
3250/8250 |
||||
Y-axis linear motor power (continuous/max.) |
|
|
|
||||
Z-axis linear motor power (continuous/max.) |
2R40*20 (screw) |
2R40*20 (screw) |
2R40*20 (screw) |
||||
Accuracy |
Positioning accuracy |
0.005/300 |
0.005/300 |
0.005/300 |
|||
Repeatability |
0.003/300 |
0.003/300 |
0.003/300 |
||||
Power source |
Power supply capacity |
40 |
45 |
55 |
70 |
55 |
70 |
Air pressure |
≥0.6Mpa ≥400L/min |
≥0.6Mpa ≥400L/min |
≥0.6Mpa ≥400L/min |
||||
Machine size |
Machine size |
2230*3403*3070 |
2800*5081*3500 |
2800*5081*3500 |
|||
Machine size (including chip conveyor and other peripheral equipment) |
2230*5540*3070 |
2800*7205*3500 |
2800*7205*3500 |
||||
Weight |
11T |
15T |
15.5T |
Processing Cases
1.Automotive Industry
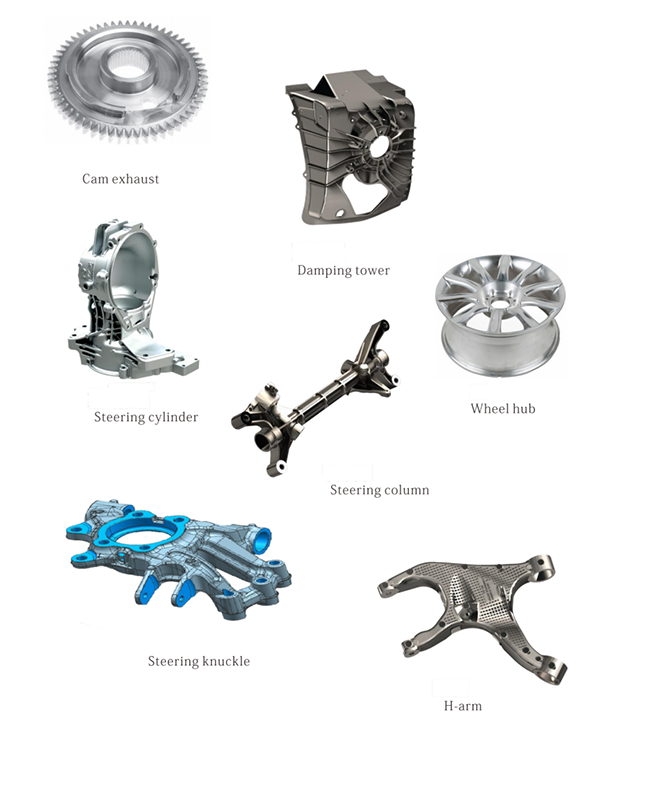
2.Aerospace
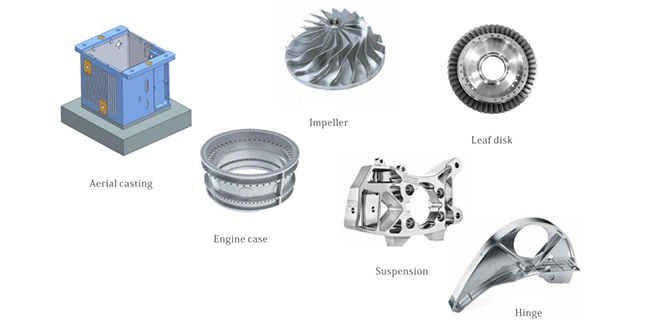
3.Construction Machinery
