Dual-Spindle CNC Lathe SK32
Product Configuration
Product Overview
The Dual-Spindle CNC Lathe is a special machine tool designed for high-efficiency and multi-process machining. It features a 30° inclined bed layout, combined with a high-rigidity cast iron structure and precision linear roller guideways. These features significantly enhance the machine's stability and chip removal efficiency. Its dual-channel control system allows for synchronized or independent spindle operations. This enables flexible simultaneous or sequential machining of both ends of workpieces. The lathe is ideal for the high-efficiency production of precision shafts, sleeves, and complex components. It meets the stringent demands of industries such as automotive, electronics, and general machinery.
Features
High-Rigidity Inclined Bed Design:
30° inclined monolithic cast bed improves rigidity, optimizes chip evacuation, and ensures stability under heavy cutting conditions while maintaining a clean workspace.
Dual-Channel Intelligent Control:
Dual spindles operate synchronously or independently, enabling multi-process machining (e.g., turning, drilling, tapping) on both ends of parts, reducing clamping cycles and boosting efficiency by over 30%.
Parameters such as clamping method, axial length, and through-hole diameter can be individually configured to adapt to various workpieces (max. clamping diameter: φ32mm).
Precision Machining & Flexibility:
Precision linear roller guideways (X/Z-axis) and a servo tailstock ensure repeat positioning accuracy of 0.006mm (X-axis) and surface roughness as low as Ra 0.4–0.8 (aluminum/steel).
Hydraulic turret with 8 stations (square/round tool holders and clamping blades) supports multi-process integration and rapid tool changes.
High-Efficiency Adaptability:
Automatic rear chip removal and fully enclosed protection ensure stable continuous production and operational safety.
Modular design accommodates machining lengths of 370–600mm, suitable for both small-batch and high-volume production.
Conclusion:
In the layout of 30 ° inclined body, the machine tool has a good rigidity and makes chip removal easier.
The dual-channel control system may be linked with the spindle simultaneously or separately, thus completing simultaneous or sequential processing of both ends of the parts.
The clamping method, axial length, through-hole diameter, and clamping diameter can be selected separately.
Applications
Industries: Automotive components, precision electronics, general machinery, hydraulic component manufacturing.
Typical Scenarios:
Automotive: Synchronized turning and drilling of transmission shafts and gear shafts.
Electronics: High-precision machining of micro-motor shafts and sensor housings.
Hydraulics: Multi-process forming of pump cores and sleeve components.
General Machinery: Batch production and refurbishment of precision shaft parts.
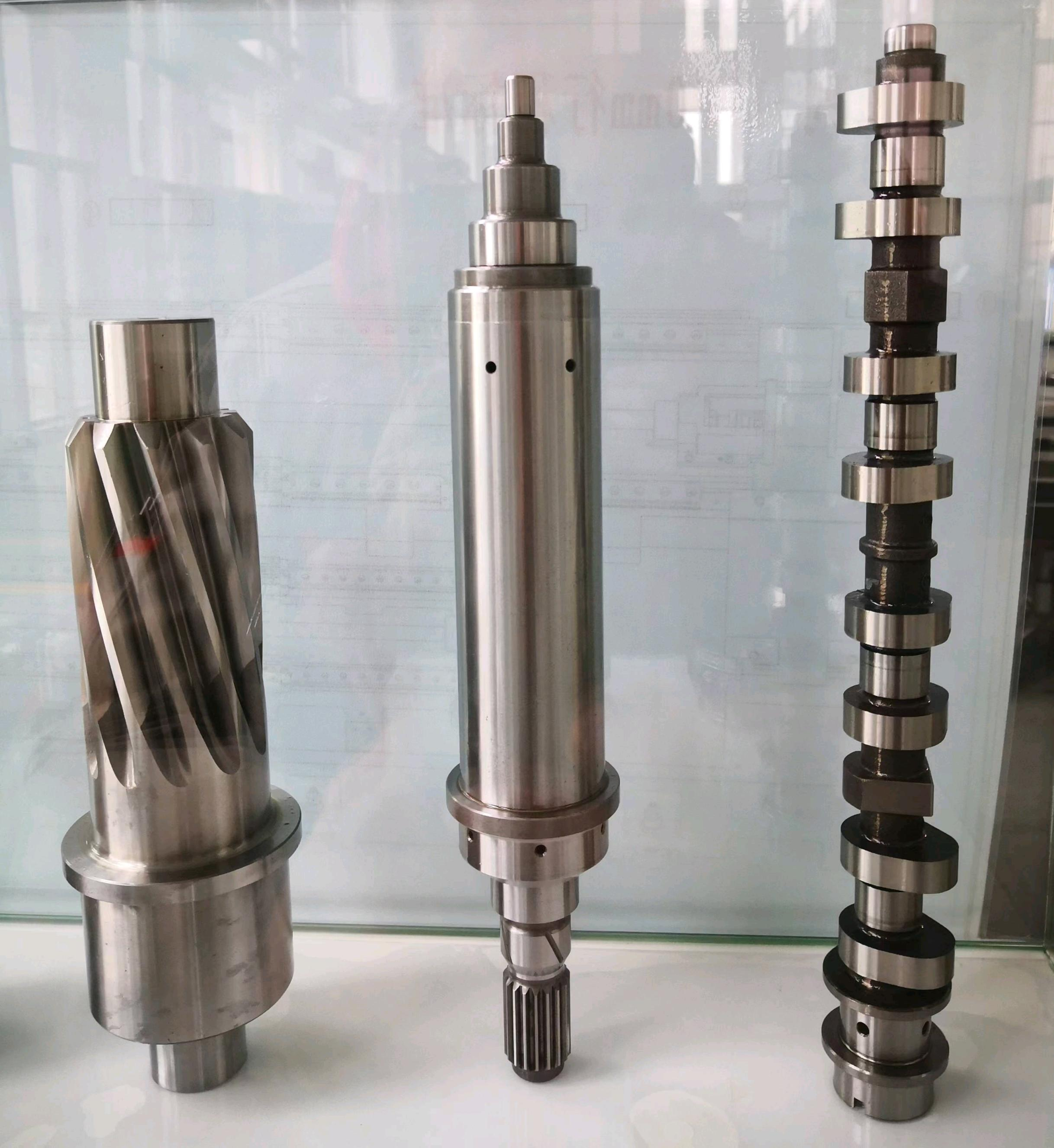
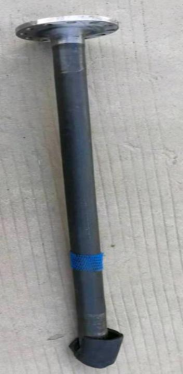
Technical Specifications
Parameter |
Request |
||
Bed |
Bed Configuration |
The bed and bed base are of standard 30° cast iron construction. |
|
Guideway |
X/Z Guideway Form |
Precision Linear Roller Guideways |
|
Y-Axis (Tailstock) Guideway Form |
|||
Working range |
Maximum Machining Diameter |
Shaft: φ32mm |
|
Processing Length |
370-600mm |
||
Maximum Tip Distance |
1155mm |
||
X/Z/Y-Axis |
Travel |
X/Z-Axis |
150mm/200mm |
Y-Axis(Tailstock) |
Left: 200mm; Right: 590mm |
||
Fast Moving Speed |
X/Z/Y-Axis |
16m/Min16m/Min10m/Min |
|
Motor Rated Torque |
X/Z/Y-Axis |
7.7NM7.7NM6NM |
|
Repetitive positioning precision(/300mm) |
X/Z/Y-Axis |
0.006mm0.01mm0.015mm |
|
Clamp |
Power Output (Continuous) |
3KW (maximum speed 2000r/min) |
|
Specification |
JHP-32(255):Maximum clamping O.D. φ32mm |
||
Transmission Method |
Synchronous Belt |
||
Turret |
Turret Forms and Specifications |
Hydraulic turret: 63-8T (228) |
|
Tool Capacity |
8 (2 square tool holders, 2 round hole tool holders, 4 clamping blades) |
||
Tool Size |
Square tool holder 20mmx20mm, round hole Φ25mm |
||
Tailstock |
Tailstock Type |
1.left/right: servo tailstock + built-in movable centre |
|
Tailstock Sleeve Type |
Fixed non-stretchable |
||
Tailstock hole of sleeve |
Mo 4# |
||
Chip Removal |
Chip Removal Type |
Automatic Rear |
|
Machining Accuracy |
Roundness |
0.005mm |
|
Diameter Consistency |
0.015mm/300mm |
||
Flatness |
0.015mm/300mm |
||
Surface Roughness (Aluminum/Steel) |
0.4HRa~0.8HRa |
||
Forms of protection |
Fully Enclosed Outer Shroud + Inner Full Protection |
|
|
Size |
Machine size(Length*Width*Height) |
2650x1900(2800)x1700 |