CNC lathe-106/108/208 Series
Product Configuration
Introduce
Turret Design Performance
The integrated positive Y-axis structure is highly rigid, heavy-duty, and has better performance than the interpolation Y-axis.
·Smoother and smoother plane contour processing
·Easier to process compound curved surfaces and contours
Compared with the "interpolation Y", the "positive Y" has obvious advantages in plane milling. The "positive Y" Y-axis movement is perpendicular to the X-axis and is a single-axis movement. The "interpolation Y" Y-axis movement is to interpolate a straight line through the simultaneous movement of the X-axis and the Y-axis. Compared with the "positive Y" for the flatness of the milling plane, the "positive Y" axis processing is obviously bright and smooth.
Direct Drive Synchronous Electric Spindle
High rigidity, high torque, higher efficiency, better finish, more precise indexing.
All major machine parts are made of cast iron HT300 with extremely strong shock absorption capacity.
Features of machine tools with direct-drive electric spindles
●Magnetic ring incremental encoder (sine and cosine) positioning accuracy: 20 arc seconds,
C-axis indexing accuracy: 40 arc seconds
●Fast start-stop response speed, saving machine tool time and effectively improving production capacity
●Small cutting load, energy saving and power saving, better protection of machine tools and extended service life
●Effectively eliminate spindle vibration, good balancing effect, good finish, and improve the surface finish of workpieces
(Advantages of turning instead of grinding, hard turning appearance, surface roughness Ra 0.2μm)
· The spindle motor is equipped with a cooling system to suppress the influence of thermal displacement and ensure that the spindle continues to work at a constant temperature.
(The nose end runout accuracy is within 0.002mm, ensuring more stable accuracy)
· Rear-mounted direct-drive synchronous spindle, more convenient installation and maintenance
· A2-5: 7016AC-front two rear two
· A2-6: front NN3020+100BAR10S, rear NN3018
A2-8: front NN3024+BT022B*2, rear NN3022
Heavy-Duty Cast Iron Base And Components
All castings are optimized using finite element analysis (FEA) to reduce distortion and lift-off shock absorption capacity. The castings of the major series of lathes are reinforced with ribs to enhance rigidity and thermal stability. Compact and symmetrical headstock and tailstock castings further enhance rigidity and ensure high positioning accuracy and repeatability.
Technical Specifications
Item |
Name |
Unit |
106 |
108 |
106M |
108M |
106MY |
108MY |
Travel |
Max. bed rotation diameter |
mm |
Φ600 |
Φ600 |
Φ600 |
Φ600 |
Φ660 |
Φ660 |
Max. machining diameter |
mm |
Φ380 |
Φ380 |
Φ310 |
Φ310 |
Φ330 |
Φ330 |
|
Max. rotation diameter on tool holder |
mm |
Φ200 |
Φ200 |
Φ200 |
Φ200 |
Φ350 |
Φ350 |
|
Max. processing length |
mm |
380 |
370 |
340 |
320 |
240 |
210 |
|
Distance between two centers |
mm |
450 |
450 |
450 |
450 |
450 |
450 |
|
Spindle Cylinder Chuck |
Spindle nose |
ASA |
A2-5 |
A2-6 |
A2-5 |
A2-6 |
A2-5 |
A2-6 |
Hydraulic cylinder/chuck |
Inch |
6’’ |
8’’ |
6’’ |
8’’ |
6’’ |
8’’ |
|
Spindle through hole diameter |
mm |
Φ56 |
Φ79/66 |
Φ56 |
Φ79/66 |
Φ66 |
Φ79/66 |
|
Max. rod through hole diameter |
mm |
Φ46 |
Φ65/52 |
Φ46 |
Φ65/52 |
Φ45 |
Φ65/52 |
|
Spindle Max. speed |
rpm |
5500 |
4300/ 4500 |
5500 |
4300 |
5500 |
4300 |
|
Spindle motor power |
kw |
17.5 |
11/15 (18/22) |
17.5 |
18/22 |
17.5 |
18/22 |
|
Spindle motor torque |
Nm |
62-125 |
91-227 (73/165) |
62-125 |
91-227 |
62-125 |
91-227 |
|
X/ZN/S Axis Feed Parameters |
X motor power |
kw |
1.8 |
1.8 |
1.8 |
1.8 |
1.8 |
1.8 |
Y motor power |
kw |
- |
- |
- |
- |
1.2 |
1.2 |
|
Z motor power |
kw |
1.8 |
1.8 |
1.8 |
1.8 |
1.8 |
1.8 |
|
X axis travel |
mm |
207 |
207 |
200 |
200 |
210 |
210 |
|
Y axis travel |
mm |
- |
- |
- |
- |
90±45 |
90±45 |
|
Z axis travel |
mm |
433 |
422 |
420 |
400 |
320 |
290 |
|
X/Z axis rail specifications |
spec |
35 roller |
35 roller |
35 roller |
35 roller |
35 roller |
35 roller |
|
Y axis rail specifications |
spec |
- |
- |
- |
- |
25 roller |
25 roller |
|
X axis fast move |
Mm/min |
30 |
30 |
30 |
30 |
24 |
24 |
|
Y axis fast move |
Mm/min |
- |
- |
- |
- |
8 |
8 |
|
Z axis fast move |
Mm/min |
30 |
30 |
30 |
30 |
24 |
24 |
|
Servo Power Turret Parameters |
Power turret type |
/ |
Servo turret |
Servo turret |
BMT45 |
BMT45 |
BMT45 |
BMT45 |
Tool station |
/ |
12T |
12T |
12T |
12T |
12T |
12T |
|
M motor power |
kw |
- |
- |
5.5 |
5.5 |
5.5 |
5.5 |
|
M axis motor torque |
Nm |
- |
- |
35 |
35 |
35 |
35 |
|
Power head Max. speed |
rpm |
- |
- |
6000 |
6000 |
6000 |
6000 |
|
Outer diameter tool holder specifications |
mm |
25*25 |
25*25 |
20*20 |
25*25 |
25*25 |
25*25 |
|
Inner diameter tool holder specifications |
mm |
Φ40 |
Φ40 |
Φ40 |
Φ40 |
Φ40 |
Φ40 |
|
Adjacent tool change time |
sec |
0.15 |
0.15 |
0.15 |
0.15 |
0.15 |
0.15 |
|
Positioning accuracy |
/ |
±2” |
±2” |
±2” |
±2” |
±2” |
±2” |
|
Repeat positioning accuracy |
/ |
±1” |
±1” |
±1” |
±1” |
±1” |
±1” |
|
Tailstock Parameters |
Programmable hydraulic tailstock |
/ |
Hydraulic program tailstock |
Hydraulic program tailstock |
Hydraulic program tailstock |
Hydraulic program tailstock |
Hydraulic program tailstock |
Hydraulic program tailstock |
Tailstock Max. travel |
mm |
360 |
360 |
360 |
360 |
360 |
360 |
|
Sleeve diameter |
mm |
Φ80 |
Φ80 |
Φ80 |
Φ80 |
Φ80 |
Φ80 |
|
Sleeve travel |
mm |
100 |
100 |
100 |
100 |
100 |
100 |
|
Sleeve taper |
/ |
MT4# |
MT4# |
MT4# |
MT4# |
MT4# |
MT4# |
|
Dimensions |
Overall dimensions |
m |
2200*2000*1800 |
2400*2000*1800 |
2200*2000*1800 |
2400*2000*1900 |
2200*2000*1800 |
2400*2000*1900 |
Machine weight approx. |
kg |
3600 |
3700 |
3700 |
3800 |
3800 |
3800 |
|
Other |
Cutting fluid tank volume |
L |
150 |
150 |
150 |
150 |
150 |
150 |
Cooling water pump power |
kw |
0.75 |
0.75 |
0.75 |
0.75 |
0.75 |
0.75 |
|
Hydraulic unit box volume |
L |
40 |
40 |
40 |
40 |
40 |
40 |
|
Hydraulic oil pump motor power |
kw |
1.5 |
1.5 |
1.5 |
1.5 |
1.5 |
1.5 |
|
Lubricating oil tank volume |
L |
2 |
2 |
2 |
2 |
2 |
2 |
|
Automatic lubrication pump motor power |
kw |
50 |
50 |
50 |
50 |
50 |
50 |
Item |
Name |
Unit |
208 |
208M |
208MY |
Travel |
Max. bed rotation diameter |
mm |
Φ620 |
Φ620 |
Φ700 |
Max. machining diameter |
mm |
Φ510 |
Φ510 |
Φ420 |
|
Max. rotation diameter on tool holder |
mm |
Φ300 |
Φ300 |
Φ300 |
|
Max. processing length |
mm |
520 |
420 |
360 |
|
Distance between two centers |
mm |
600 |
600 |
600 |
|
Spindle Cylinder Chuck |
Spindle nose |
ASA |
A2-6 |
A2-6 |
A2-6 |
Hydraulic cylinder/chuck |
Inch |
8’’ |
8’’ |
8’’ |
|
Spindle through hole diameter |
mm |
Φ79/66 |
Φ79/66 |
Φ79/66 |
|
Max. rod through hole diameter |
mm |
Φ65/52 |
Φ65/52 |
Φ65/52 |
|
Spindle Max. speed |
rpm |
4000/4300 |
4300 |
4300 |
|
Spindle motor power |
kw |
18/22(11/15) |
18/22 |
18/22 |
|
Spindle motor torque |
Nm |
91-227 (73/165) |
91-227 (73/165) |
91-227 |
|
Sub-Spindle Cylinder Chuck
|
Sub-Spindle nose |
ASA |
- |
- |
- |
Sub-Hydraulic cylinder/chuck |
Inch |
- |
- |
- |
|
Sub-Spindle through hole diameter |
mm |
- |
- |
- |
|
Sub-Max. rod through hole diameter |
mm |
- |
- |
- |
|
Sub-Spindle Max. speed |
rpm |
- |
- |
- |
|
Sub-Spindle motor power |
kw |
- |
- |
- |
|
X/ZN/S Axis Feed Parameters |
X motor power |
kw |
3.0 |
3.0 |
2.5 |
Y motor power |
kw |
- |
- |
1.2 |
|
Z motor power |
kw |
3.0 |
3.0 |
2.5 |
|
S motor power |
Kw |
- |
- |
- |
|
X axis travel |
mm |
272 |
216 |
262 |
|
Y axis travel |
mm |
- |
- |
100±50 |
|
Z axis travel |
mm |
570 |
500 |
450 |
|
X/Z axis rail specifications |
spec |
35 roller |
35 roller |
35 roller |
|
Y axis rail specifications |
spec |
- |
- |
25 roller |
|
S axis travel |
mm |
- |
- |
- |
|
X axis fast move |
Mm/min |
20 |
20 |
20 |
|
Z axis fast move |
Mm/min |
20 |
20 |
20 |
|
Y axis fast move |
Mm/min |
- |
- |
8 |
|
S axis fast move |
Mm/min |
- |
- |
- |
|
Servo power Turret Parameters |
Power turret type |
/ |
Servo turret |
BMT55 |
BMT55 |
Tool station |
/ |
12T |
12T |
12T |
|
M motor power |
kw |
- |
5.5 |
5.5 |
|
M axis motor torque |
Nm |
- |
35 |
35 |
|
Power head Max. speed |
rpm |
- |
6000 |
6000 |
|
Outer diameter tool holder specifications |
mm |
25*25 |
25*25 |
25*25 |
|
Inner diameter tool holder specifications |
mm |
Φ40 |
Φ40 |
Φ40 |
|
Adjacent tool change time |
sec |
0.15 |
0.15 |
0.15 |
|
Positioning accuracy |
/ |
±2” |
±2” |
±2” |
|
Repeat positioning accuracy |
/ |
±1” |
±1” |
±1” |
|
Tailstock Parameters |
Programmable hydraulic tailstock |
/ |
Hydraulic program tailstock |
Hydraulic program tailstock |
Hydraulic program tailstock |
Tailstock Max. travel |
mm |
440 |
440 |
440 |
|
Sleeve diameter |
mm |
Φ100 |
Φ100 |
Φ100 |
|
Sleeve travel |
mm |
100 |
100 |
100 |
|
Sleeve taper |
/ |
MT#5 |
MT#5 |
MT#5 |
|
Dimensions |
Overall dimensions |
m |
2600*2100*1800 |
2600*2100*1800 |
2700*2400*1800 |
Machine weight approx. |
kg |
5000 |
5200 |
5200 |
|
Other |
Cutting fluid tank volume |
L |
150 |
150 |
150 |
Cooling water pump power |
kw |
0.75 |
0.75 |
0.75 |
|
Hydraulic unit box volume |
L |
40 |
40 |
40 |
|
Hydraulic oil pump motor power |
kw |
1.5 |
1.5 |
1.5 |
|
Lubricating oil tank volume |
L |
2 |
2 |
2 |
|
Automatic lubrication pump motor power |
kw |
50 |
50 |
50 |
Configuration Introduction
Easier To Use And More Powerful
●Fully upgraded design
●Equipped with i HMI
●Equipped with FANUC's latest CNC and servo technology
●Standardized with personalized functions
●Expanded memory capacity
Ease Of Use
Prevent sudden machine downtime through preventive maintenance
●Rich fault prediction functions
Easily locate the fault location and shorten recovery time
●Diagnosis/maintenance functions
High processing performance
Shortened Cycle Time
●High-efficiency processing technology
Achieve high-quality processing
Surface fine processing technology
●Diagnosis/maintenance function
High Operation Rate
Always support various operations at the processing site
●FANUC
Personalized Screen Is Easier To Use
●Standardized personalized function
Initiatives in the field of IoT
●Support for a wide range of on-site networks
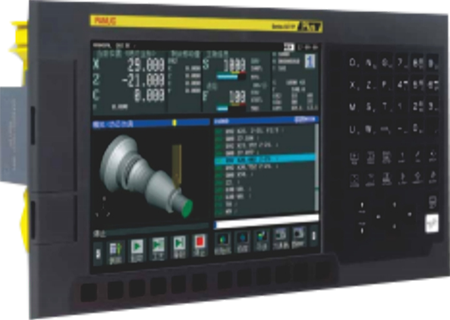
THK Ball Screw
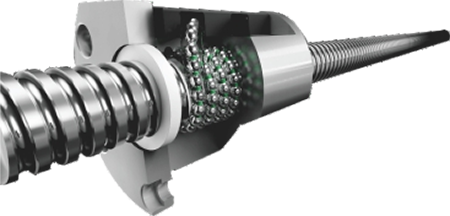
·C3 grade, using high-precision ball screw, with nut pre-loading and screw pre-tensioning treatment to pre-eliminate backlash and temperature rise elongation, showing excellent positioning and repeatability accuracy.
·Servo motor direct drive to reduce backlash error.
THK Roller Linear Guide
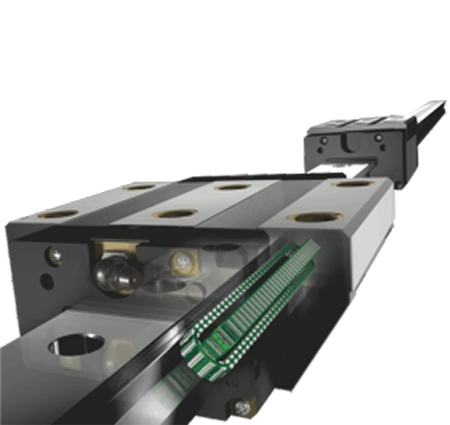
·P grade ultra-high rigidity SRG precision grade, linear guide zero clearance, arc cutting, bevel cutting, surface texture is relatively uniform. Suitable for high-speed operation, greatly reducing the driving horsepower required for machine tools.
·Rolling instead of sliding, small friction loss, sensitive response, high positioning accuracy. It can bear the load in the moving direction at the same time, and the track contact surface is still in multi-point contact during the load, and the cutting rigidity will not be reduced.
·Easy to assemble, strong interchangeability, and simple lubrication structure; the wear amount is very small and the service life is long.
SKF Bearing/Oiling Machine
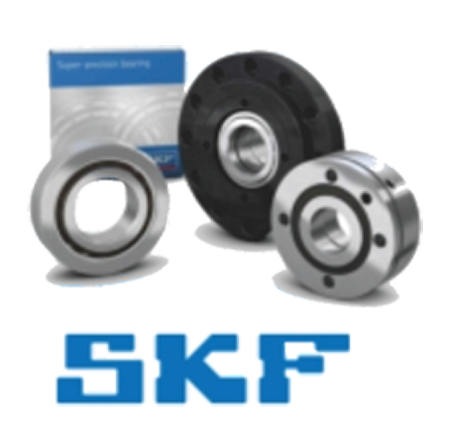
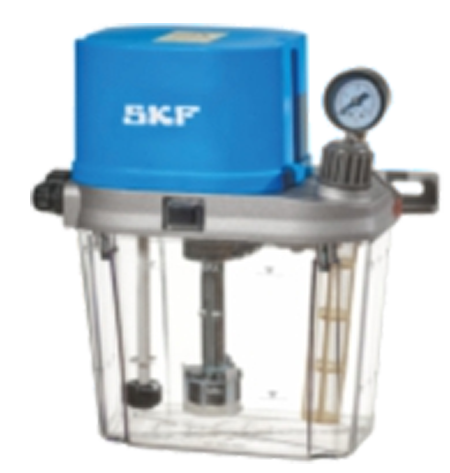
·Automatic lubricator meets the needs of various applications, suitable for various working conditions, reliable products, flexible use.
·Meet the needs of bearing lubrication in high temperature, strong vibration and dangerous environment.
Each lubrication point uses a volumetric proportional distributor to control the lubrication amount, and the machine can be controlled by PLC to accurately supply oil.