CNC Double Spindle Turning Center 150MS Series
Product Configuration
Introduce
1. Adopt direct drive synchronous electric spindle device: magnetic ring incremental encoder (sine and cosine) positioning accuracy: 20 arc seconds, C-axis indexing accuracy: 40 arc seconds. ①Effectively eliminate spindle vibration, and the nose deflection accuracy is within 0.002MM. Improve the surface finish of the workpiece, ② adopt a rear-mounted rotor, which makes installation and maintenance faster, ③ the spindle motor is equipped with a cooling system to suppress the influence of thermal displacement and ensure a constant operating temperature of the spindle. The spindle system has undergone strict dynamic balance testing. Its good accuracy retention, high rigidity and high efficiency enable the whole machine to not only complete finishing, but also perform rough machining and heavy cutting for users. It is especially suitable for mass production of complex shapes and high smoothness. product.
2. High rigidity integrated design servo power turret. It helps the servo turret's rapid and accurate tool changing performance, and when coupled with the power milling of a high-speed power axis, it achieves excellent turning and milling combined processing capabilities. The tool holder is installed with a high-rigidity BMT installation interface, and the power transmission shaft is driven by a servo spindle motor.
3. The machine tool is equipped with linear guide rails and precision ground ball screws to ensure the best accuracy and durability. Each axis adopts a direct transfer axis structure and a double-anchor pre-relay method, which can minimize the amount of thermal displacement and significantly Improve processing accuracy. The high-rigidity, large-sized, heavy-duty linear slide rails maintain intact accuracy when the machine is subjected to impact, and the displacement is smooth and low-noise, which can extend the service life.
4. This machine provides users with a complete hydraulic and lubrication system, using high-quality hydraulic pumps, hydraulic valves and other components to greatly reduce the failure rate. The hydraulic and lubrication systems are designed to be simple and reliable. The machine tool adopts centralized quantitative automatic lubrication.
5. It adopts Taiwan rotary cylinder and optional automatic chip removal device. The options are divided into rear row and side row, which can greatly reduce the labor intensity of the operator and achieve safe and efficient production. The above functional components can all be programmed to control, and are designed with oil-water separation and iron cutting filtering devices. At the same time, various special fixtures can be designed and installed according to the special requirements of users.
Technical Specifications
Item Model |
Name |
Unit |
150MSY-II |
150MSY-III |
150MS-II |
150MS-III |
Travel |
Max. bed rotation diameter |
mm |
Ф380 |
Ф380 |
Ф380 |
Ф380 |
Max. processing diameter |
mm |
Ф100 |
Ф100 |
Ф100 |
Ф100 |
|
Max. processing diameter on tool holder |
mm |
Ф160 |
Ф160 |
Ф160 |
Ф160 |
|
Max. processing length |
mm |
150 |
150 |
150 |
150 |
|
Spindle Cylinder Chuck |
Spindle nose |
/ |
A2-5 |
A2-5 |
A2-5 |
A2-5 |
Max. speed of spindle |
mm |
5500 |
5500 |
5500 |
5500 |
|
Spindle hydraulic cylinder/colletHydraulic Cylinder/Chuck |
rpm |
6" |
6" |
6" |
6" |
|
Spindle hole diameter Spindle hole diameter |
kw |
Ф56 |
Ф56 |
Ф56 |
Ф56 |
|
Max. bar hole diameter of spindle Bar diameter |
Nm |
Ф45 |
Ф45 |
Ф45 |
Ф45 |
|
Spindle motor power |
/ |
17.5 |
17.5 |
17.5 |
17.5 |
|
Spindle motor power |
|
62-125 |
62-125 |
62-125 |
62-125 |
|
Sub-spindle Chuck |
Sub-spindle nose |
/ |
A2-4 |
A2-4 |
A2-4 |
A2-4 |
Max. speed of sub-spindle |
mm |
6000 |
6000 |
6000 |
6000 |
|
Sub-spindle hydraulic cylinder/collet H |
rpm |
5" |
5" |
5" |
5" |
|
Sub-spindle through hole diameter |
Nm |
Ф46 |
Ф46 |
Ф46 |
Ф46 |
|
Max. bar hole diameter of sub-spindle |
kw |
Ф32 |
Ф32 |
Ф32 |
Ф32 |
|
Direct drive electric spindle power |
/ |
11 |
11 |
11 |
11 |
|
Spindle direct drive motor torque |
|
27-66 |
27-66 |
27-66 |
27-66 |
|
X1/Z1/Y/X2/Z2 axis feed parameter |
X1/Z1/Y motor power |
kw |
1.8/1.2/1.2 |
1.8/1.2/1.2 |
1.8/1.2 |
1.8/1.2 |
X2/Z2 motor power |
mm |
1.2/1.2 |
1.2/1.2 |
1.2/1.2 |
1.2/1.2 |
|
X1/Z1 axis travel |
mm |
135/370 |
135/370 |
135/370 |
135/370 |
|
X2/Z2 axis travel |
mm/min |
215/400 |
215/400 |
215/400 |
215/400 |
|
X/Z//Y/S axis rapid movement |
mm |
30/30/6/30 |
30/30/6/30 |
30/30/30 |
30/30/30 |
|
X1/Z1 slide rail type |
mm |
Roller35/35 |
Roller35/35 |
Roller35/35 |
Roller35/35 |
|
X2/Z2 slide rail type |
mm |
Roller30/30 |
Roller30/30 |
Roller30/30 |
Roller30/30 |
|
Servo drive Cutter parameters |
Turret type |
pcs |
BMT45-12T |
BMT45-12T |
BMT45-12T |
BMT45-12T |
Power turret power |
Kw/Nm |
2.2/26Nm |
2.2/26Nm |
2.2/26Nm |
2.2/26Nm |
|
Y axis travel |
mm |
80(±40) |
80(±40) |
|
6000 ER20 |
|
Max. speed of driven tool holder |
rpm |
6000 ER20 |
6000 ER20 |
6000 ER20 |
20x20 |
|
Outside diameter tool holder specifications |
mm |
20x20 |
20x20 |
20x20 |
Ф32 |
|
Inner diameter tool holder specifications |
mm |
Ф32 |
Ф32 |
Ф32 |
0.15 |
|
Adjacent tool change time |
sec |
0.15 |
0.15 |
0.15 |
BMT40-8T |
|
Servo power Turret parameters |
Power turret type |
/ |
NC8T |
BMT40-8T |
NC8T |
2.2/26Nm |
Outer diameter tool holder specifications |
mm |
25x25 |
20x20 |
25x25 |
6000 ER20 |
|
Inner diameter tool holder specifications |
mm |
Ф32 |
Ф32 |
Ф32 |
20x20 |
|
Adjacent tool change time |
sec |
0.15 |
0.15 |
0.15 |
Ф25 |
|
Dimensions |
Occupied area Approx. |
mm |
2.2x2.1x1.7 |
2.2x2.1x1.7 |
2.2x2.1x1.7 |
0.15 |
Machine weight Approx. |
kg |
3500 |
3500 |
3200 |
2.2x2.1x1.7 |
|
Other |
Cutting fluid tank volume |
L |
180 |
180 |
180 |
3500 |
Hydraulic unit box volume |
L |
40 |
40 |
40 |
180 |
|
Hydraulic oil pump motor power |
kw |
1.5 |
1.5 |
1.5 |
40 |
|
Lubricating oil tank volume |
L |
2 |
2 |
2 |
1.5 |
|
Automatic lubrication pump motor power |
W |
50 |
50 |
50 |
2 |
|
Cooling water pump power |
W |
750 |
750 |
750 |
50 |
Configuration Features
Easier To Use And More Powerful
●Fully upgraded design
●Equipped with i HMI
●Equipped with FANUC's latest CNC and servo technology
●Standardized with personalized functions
●Expanded memory capacity
Ease Of Use
Prevent sudden machine downtime through preventive maintenance
●Rich fault prediction functions
Easily locate the fault location and shorten recovery time
●Diagnosis/maintenance functions
High processing performance
Shortened Cycle Time
●High-efficiency processing technology
Achieve high-quality processing
Surface fine processing technology
●Diagnosis/maintenance function
High Operation Rate
Always support various operations at the processing site
●FANUC
Personalized Screen Is Easier To Use
●Standardized personalized function
Initiatives in the field of IoT
●Support for a wide range of on-site networks
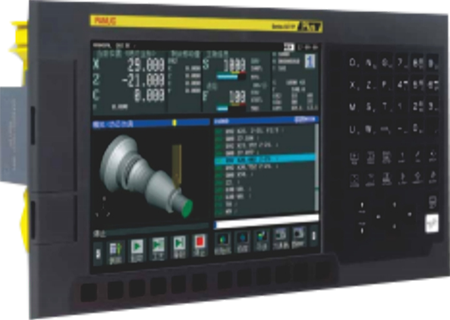
THK Ball Screw
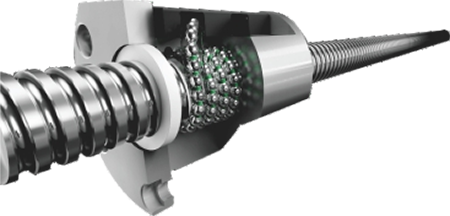
·C3 grade, using high-precision ball screw, with nut pre-loading and screw pre-tensioning treatment to pre-eliminate backlash and temperature rise elongation, showing excellent positioning and repeatability accuracy.
·Servo motor direct drive to reduce backlash error.
THK Roller Linear Guide
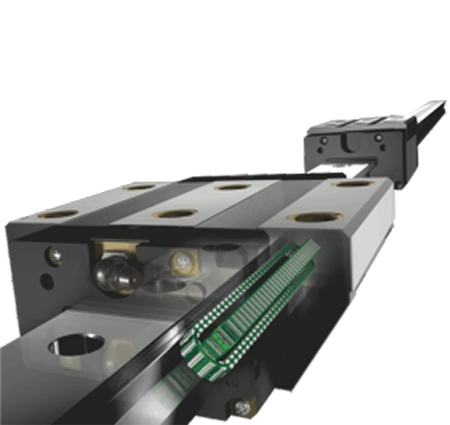
·P grade ultra-high rigidity SRG precision grade, linear guide zero clearance, arc cutting, bevel cutting, surface texture is relatively uniform. Suitable for high-speed operation, greatly reducing the driving horsepower required for machine tools.
·Rolling instead of sliding, small friction loss, sensitive response, high positioning accuracy. It can bear the load in the moving direction at the same time, and the track contact surface is still in multi-point contact during the load, and the cutting rigidity will not be reduced.
·Easy to assemble, strong interchangeability, and simple lubrication structure; the wear amount is very small and the service life is long.
SKF Bearing/Oiling Machine
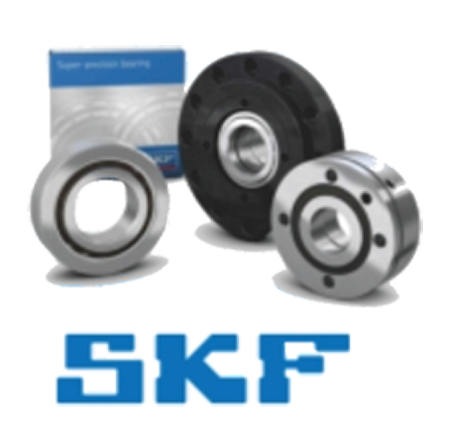
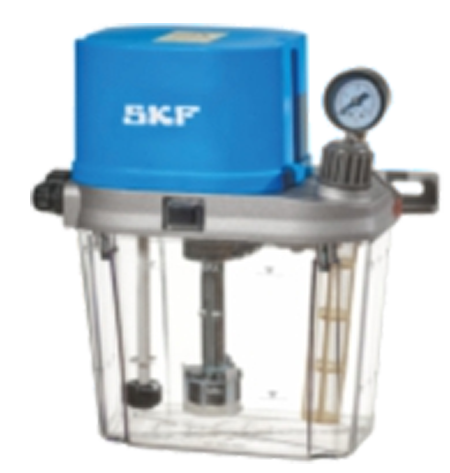
·Automatic lubricator meets the needs of various applications, suitable for various working conditions, reliable products, flexible use.
·Meet the needs of bearing lubrication in high temperature, strong vibration and dangerous environment.
Each lubrication point uses a volumetric proportional distributor to control the lubrication amount, and the machine can be controlled by PLC to accurately supply oil.